Course Description
Turning Tool and Process Basics gives learners insight on the cutting tool, workholding device, and cutting operation selection process for turning centers. These topics are tailored to a level appropriate for a CNC turning center setup operator, and industry professionals seeking to understand the job functions of this role. Combining live video with animated demonstrations, this course covers everything from cutting parameters, to L/D ratio and workholding selection, to the format of canned cycles in CNC programming.
Who will benefit from this Machining Turning Tools Basics course?
Manufacturing, quality, and engineering functions in an organization that seeks to understand the process of turning.
Course Classification
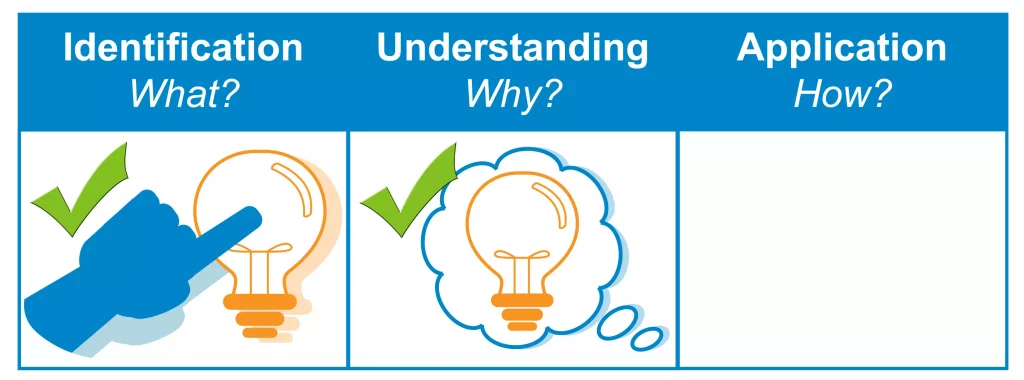
*THORS uses the Bloom’s Taxonomy Methodology for our course development.
Certificate Awarded for Turning Tool and Process Basics

*upon successful completion
Related Posts
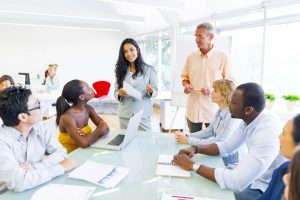
5 signs you should invest in effective workforce training
In today’s constantly changing marketplace, the importance of workforce training has never been greater. Workforce training has the ability to not only increase workforce efficiency
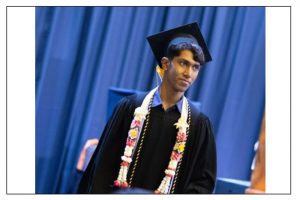
How THORS Courses Helped a Mechatronics Student in Germany
Sasshank is an international student attending University in Germany where he studies mechatronics engineering. He was born in Tamil Nadu, where he attended various schools

How Can THORS Help Enhance Your College Education?
How Can THORS Help Enhance Your College Education? THORS Academy can help enhance your college education in a number of ways. Imagine being in a