Course Description
Forgings: Closed Die Processes introduces learners to the pre-forging processes, conventional forging, and final inspection. The important and commercially vital process of closed die forging is brought to life in this course using realistic 3D models, helpful animations, and interactive quizzes. The material in this course is beneficial for both experienced forging veterans and learners new to the industry.
Who will benefit from this Closed Die Forging course?
Procurement, supplier quality, engineers, and operations personnel who purchase closed die forgings; Operations, quality, sales, engineering, and customer service personnel who produce closed die forgings; Product design engineers and manufacturing engineers looking to optimize the material specifications between open forgings, castings, and closed die forgings.
Course Classification

*THORS uses the Bloom’s Taxonomy Methodology for our course development.
Certificate Awarded for Forgings: Closed Die Processes

*upon successful completion
Related Posts

How Can THORS Help Enhance Your College Education?
How Can THORS Help Enhance Your College Education? THORS Academy can help enhance your college education in a number of ways. Imagine being in a
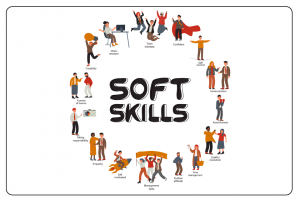
Developing Soft Skills in the Tech Industry
Soft skills in the tech industry, where precision and expertise are paramount, might seem secondary. However, soft skills such as communication, teamwork, and problem-solving, play
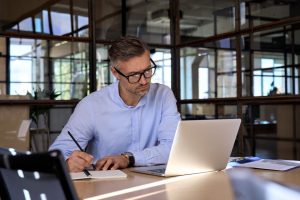
eLearning Support for On-Site Training
eLearning has emerged as a revolutionary force in the realm of learning and professional development, evolving into an imperative tool in today’s competitive landscape. The