The Job Gap Challenge
The exodus of baby boomers from the manufacturing sector has highlighted a critical challenge for employers: the job gap. This gap is not merely a numerical shortage but a complex issue that affects various facets of manufacturing operations, particularly when it comes to attracting younger workers to manufacturing jobs. It is especially pronounced in certain job roles that have traditionally relied on the deep-rooted expertise and hands-on experience of the retiring generation.
Job Roles Most Affected
The impact of baby boomer retirements is felt across the board, but certain positions are experiencing a more acute shortage. Skilled trades positions, such as machinists [https://thors.com/courses-manufacturing/machining-video-series/] welders, and maintenance technicians, are particularly hard-hit. These roles require a level of skill and experience that cannot be quickly or easily replaced. Similarly, engineering positions and specialized roles that involve managing complex manufacturing processes or advanced technology are seeing significant vacancies. The gap in these critical areas threatens not only the operational efficiency of manufacturing plants but also their innovation capacity and competitive edge.
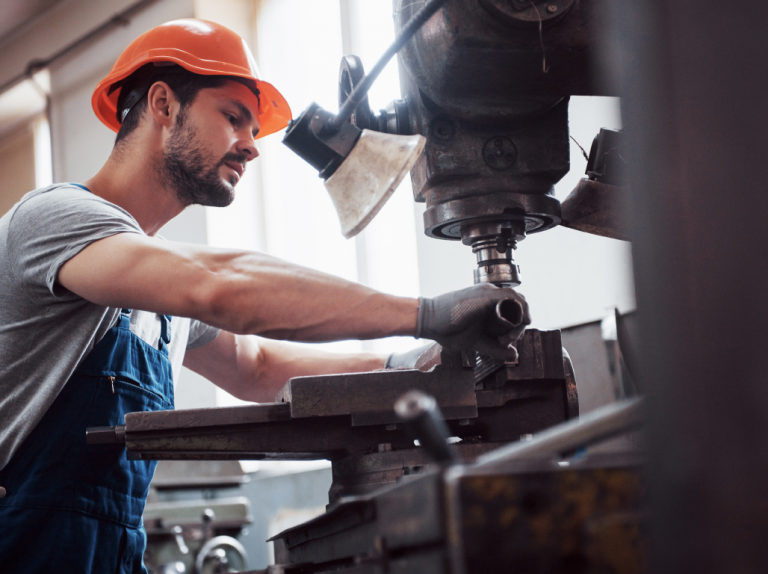
Recruiting Younger Workers: A Daunting Task
Filling these vacancies with younger workers has proven to be a formidable challenge for several reasons. First, there’s a prevailing perception issue: manufacturing careers are often mistakenly seen as outdated or lacking in advancement opportunities compared to tech-centric fields. This perception has deterred many young professionals from considering a career in manufacturing.
Additionally, the skill sets required for modern manufacturing roles have evolved. Today’s manufacturing jobs often require a blend of technical acumen, digital literacy, and soft skills—a combination that is not readily available in the workforce. The education and training systems have been slow to adapt to these changing needs, creating a mismatch between the skills employers need and those available in the job market.
The Knowledge Gap Dilemma
As the manufacturing sector navigates the challenges posed by the retirement of baby boomers, one of the most pressing concerns is the knowledge gap. This gap represents more than the loss of workers; it signifies the potential disappearance of decades’ worth of accumulated experience, insights, and nuanced understanding of manufacturing processes. The knowledge that retiring baby boomers possess is an invaluable asset, one that has been honed through years of hands-on work, problem-solving, and innovation. Additionally, “The manufacturing skills gap in the U.S. could result in 2.1 million unfilled jobs by 2030, according to a new study by Deloitte and The Manufacturing Institute, the workforce development and education partner of the NAM. The cost of those missing jobs could potentially total $1 trillion in 2030 alone.”
The Wealth of Boomer Knowledge
The retiring generation brings with them an irreplaceable depth of knowledge about everything from the intricacies of machinery and equipment to the subtleties of supply chain logistics. Their expertise extends beyond technical skills to include critical problem-solving abilities, a nuanced understanding of workflow efficiencies, and often, a rich history of the company’s evolution and market dynamics. This wealth of knowledge has been instrumental in guiding decisions, optimizing processes, and fostering innovation within the manufacturing sector.
Challenges in Knowledge Transfer
Transferring this vast repository of knowledge to the younger generation is fraught with challenges. One significant hurdle is the tacit nature of much of this knowledge. Much of what baby boomers know is not documented but resides in their experiential understanding and intuitive problem-solving strategies. Capturing and transferring this kind of knowledge requires more than traditional training programs; it demands innovative approaches to mentorship and learning.
Moreover, the pace of retirement among baby boomers often outstrips the ability of organizations to transfer their knowledge effectively. Without strategic planning, companies risk sudden departures that leave gaps not just in staffing but in the continuity of critical knowledge. From aem.org, “According to a survey of 1,500 baby boomers by Express Employment Professionals, few employers are asking for their knowledge before they leave.
- 57% of baby boomers said they had shared less than half of the knowledge needed to perform their job responsibilities with those who will assume them after they retire.
- 21% said they shared none of their knowledge.
- Only 18% felt they had shared all of their knowledge.”
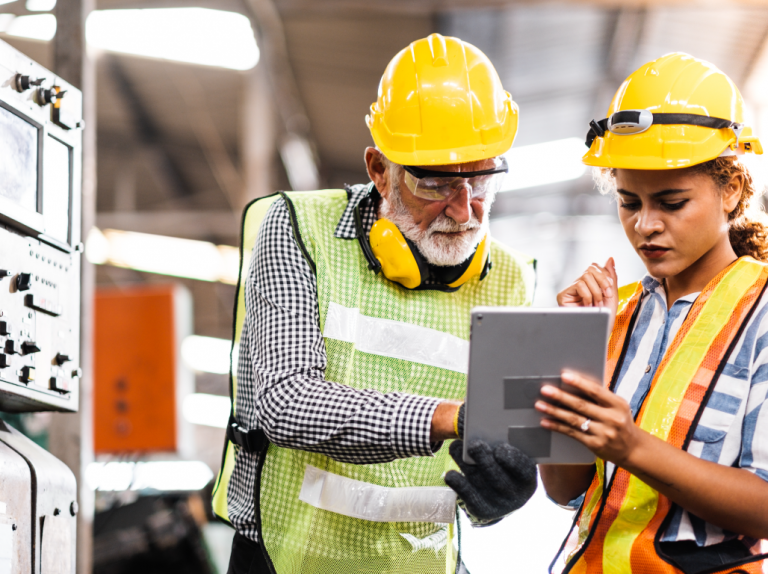
The Impact of Knowledge Loss
The consequences of failing to address the knowledge gap are far-reaching. Examples abound of companies that have experienced significant setbacks due to knowledge loss. In one instance, a manufacturing plant faced repeated equipment breakdowns that could have been prevented by the nuanced understanding of a recently retired technician. In another, the loss of a long-time procurement officer led to inefficiencies in supply chain management that significantly increased costs and delayed production. In fact, “Lack of knowledge transfer is estimated to cost large businesses $47 million per year due to time waste, missed opportunities, frustration and delayed projects,” according to aem.org.
Safety protocols, too, can suffer without the transmission of experienced-based knowledge, leading to increased workplace accidents and violations of safety standards. One scary statistic from Rockford Systems states that “…employees under the age of 25 are twice as likely to visit the emergency room for an occupational injury than those over 25.” Perhaps most critically, the erosion of deep institutional and technical knowledge can stifle innovation, as new generations of workers lack the foundational understanding necessary to drive forward-thinking solutions.
Addressing the knowledge gap dilemma requires a concerted effort by the manufacturing sector to recognize the value of baby boomer knowledge and to implement creative, effective strategies for knowledge preservation and transfer. This effort is not just about maintaining the status quo but about securing the future of manufacturing as a dynamic, innovative industry.
Strategies for Bridging the Gap
Confronted with the dual challenges of job and knowledge gaps, the manufacturing sector must adopt a multifaceted approach to ensure its vitality and competitiveness. Here are some strategies and best practices for attracting younger workers, facilitating knowledge transfer, and leveraging the expertise of retired professionals.
Attracting Younger Workers to Manufacturing Jobs
Modernizing the Image of Manufacturing: Shifting the perception of manufacturing from outdated and dirty to a field that’s innovative and tech-driven is crucial. Highlighting the use of advanced technologies such as AI, robotics, and 3D printing can appeal to the tech-savvy younger generation.
Offering Competitive Salaries and Benefits: To be competitive with other industries vying for young talent, manufacturing companies must offer attractive compensation packages, including salaries, health benefits, and career development opportunities.
Providing Training Programs: Developing apprenticeship programs, internships, and on-the-job training opportunities that allow young workers to gain skills and experience can bridge the gap between educational institutions and the manufacturing floor.
Knowledge Transfer Best Practices
Mentorship Programs: Pairing experienced workers with newcomers can facilitate the transfer of tacit knowledge that isn’t easily documented. These programs can offer structured yet flexible frameworks for sharing critical insights and skills.
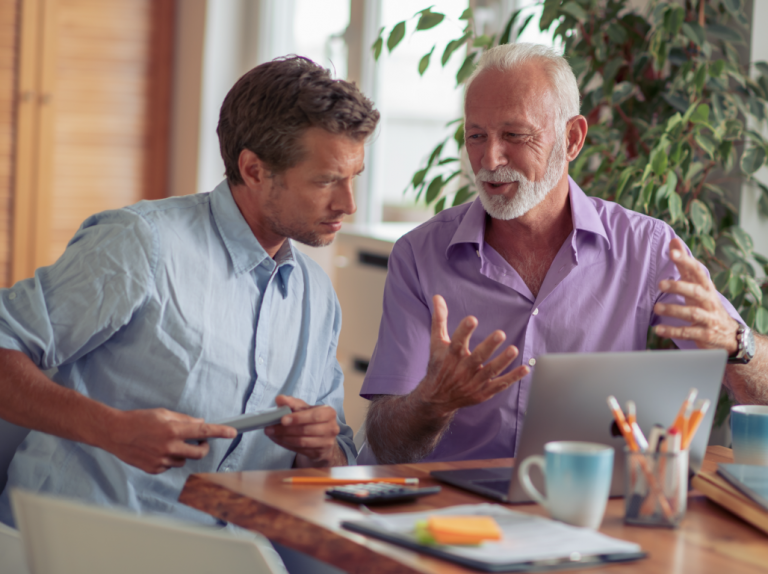
Documentation of Processes: Encouraging retiring employees to document their knowledge about processes, troubleshooting, and best practices can help preserve crucial information. This documentation can serve as a reference for training and everyday operations.
Investment in eLearning Platforms: Digital platforms can offer interactive, engaging ways to learn about manufacturing processes, safety protocols, and equipment operation. eLearning can be particularly effective in reaching younger workers accustomed to digital environments.
Retaining Baby Boomer Expertise
Advisory Roles for Retired Professionals: Inviting retired employees to serve in advisory capacities can help retain their invaluable insight and experience. These roles can be flexible, accommodating the retirees’ preferences while still benefiting the company.
Part-time Positions: Offering part-time or consultancy positions to retiring professionals can help bridge the knowledge gap. This approach allows companies to continue benefiting from the expertise of baby boomers while gradually transferring responsibilities to younger employees.
Addressing the job gap challenge in the manufacturing sector requires a proactive and multifaceted approach. As baby boomers retire, they leave behind a legacy of invaluable knowledge and expertise that cannot be easily replaced. However, by adopting strategies to attract and retain younger workers, facilitating robust knowledge transfer programs, and leveraging the expertise of retired professionals, manufacturing companies can mitigate the impact of this transition. Embracing innovative solutions such as modernizing the industry’s image, offering competitive compensation, and investing in digital learning platforms will not only bridge the current gaps but also ensure the sector’s vitality and competitiveness for the future. It’s not just about filling positions—it’s about sustaining and enhancing the wealth of knowledge and skill that drives manufacturing excellence.
This is a three-part blog! Read the next installment here.