Additive manufacturing is the technology that unites an unlikely cohort— manufacturers, hobbyists, engineers, surgeons, and scientists; mass production capability for the manufacturer, the power to create for the hobbyist, the ability to bring ideas to life for the engineer, regenerative medicine for the surgeon, and the field of endless possibilities for the scientist. Although not synonymous, additive manufacturing is commonly known as 3D printing; 3D printing has captivated the interests of the common man and the academic elite. It is a crowd-pleaser that enjoys the rare privilege of patronage from diverse disciplines.
The Ascent of Additive Manufacturing
The mode of operations of industrial manufacturing, for high-volume production of dimensionally accurate parts with fine surface finish, has been subtractive manufacturing. Subtractive manufacturing, or machining, is the removal of material from a workpiece through various machining processes. It is a relative newcomer to the industrial manufacturing scene. Additive manufacturing, which had its humble beginnings as a rapid prototyping technology, has positioned itself as a major player in the fourth industrial revolution.
“Bees were using 3D printing to build their honeycombs long before humans happened upon the technique”, remarks renowned material scientist, Mark Miodownik2. Humanity has not only caught up with nature in employing 3D printing techniques, but we are also constantly expanding its territories—from custom manufacturing helmets for SpaceX Demo-2 Mission crew1 to investigating coral biology3.
Additive Manufacturing: Abridged
Additive manufacturing builds a product layer-by-layer by gradually adding the raw material from industrial printers. A digital file of a solid part is deconstructed to produce thousands of fine layers; the layers are printed successively, each in its X–Y coordinate, and the subsequent layers are fused together, resulting in a final part. The American Society for Testing and Materials (ASTM) has classified seven families of additive manufacturing technologies.
Family
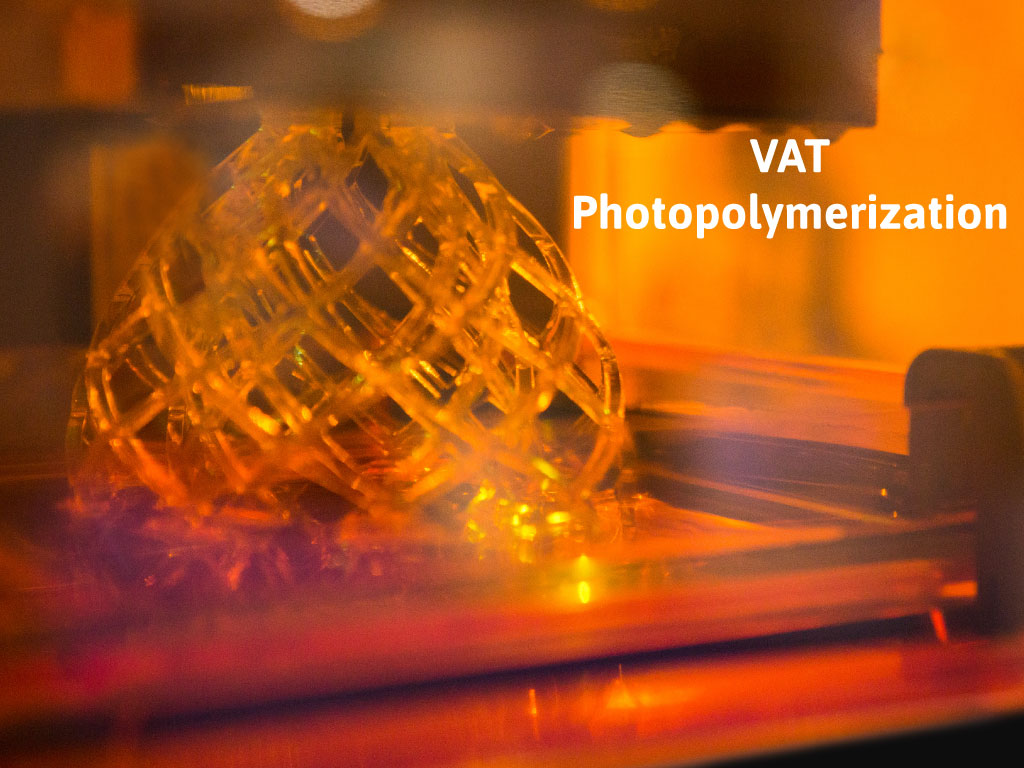
Technique
Selective curing of liquid photopolymers contained in vats using focused energy beams
Material
Liquid Photopolymer
Technologies
- Stereolithography
- Digital Light Processing
- Scan, Spin, and Selectively Photocure
- Continuous Liquid Interface Production
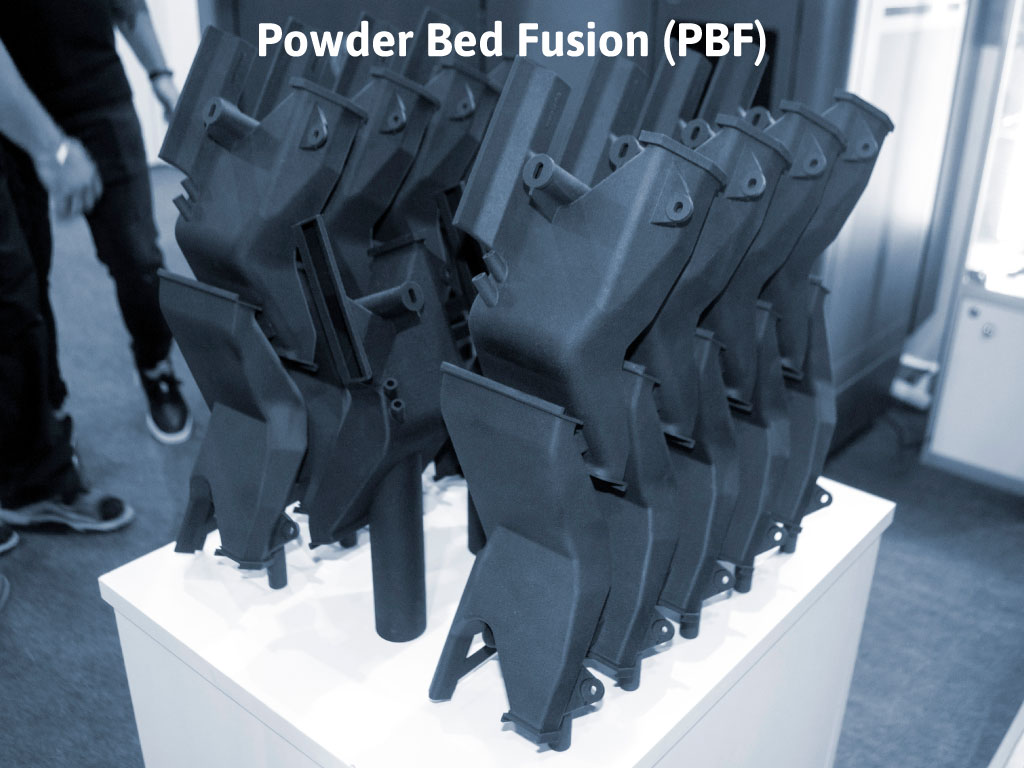
Selective sintering of powdered materials
Plastics
Metals
Ceramics
Sand
- Selective Laser Sintering
- Direct Metal Laser Sintering
- Electron Beam Melting
- Selective Heat Sintering
- Multi-Jet Fusion
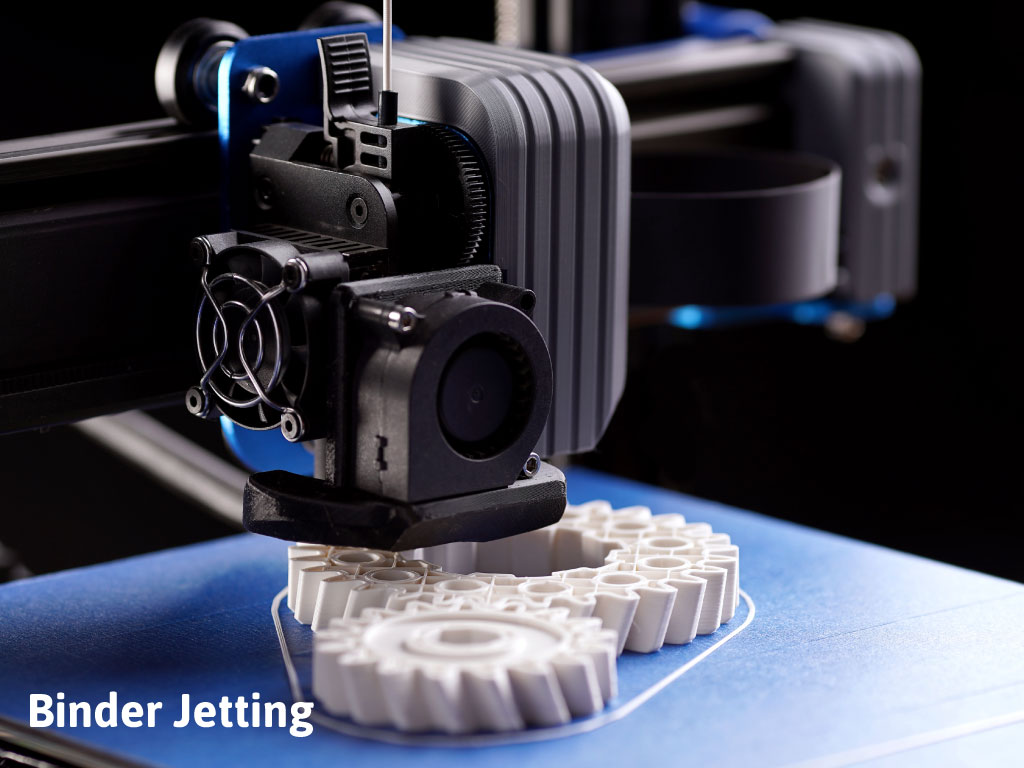
Selective application of bonding agents onto powdered material
Plastics
Metals
Ceramics
Glass
Sand
- 3D Printing
- ExOne
- Voxeljet
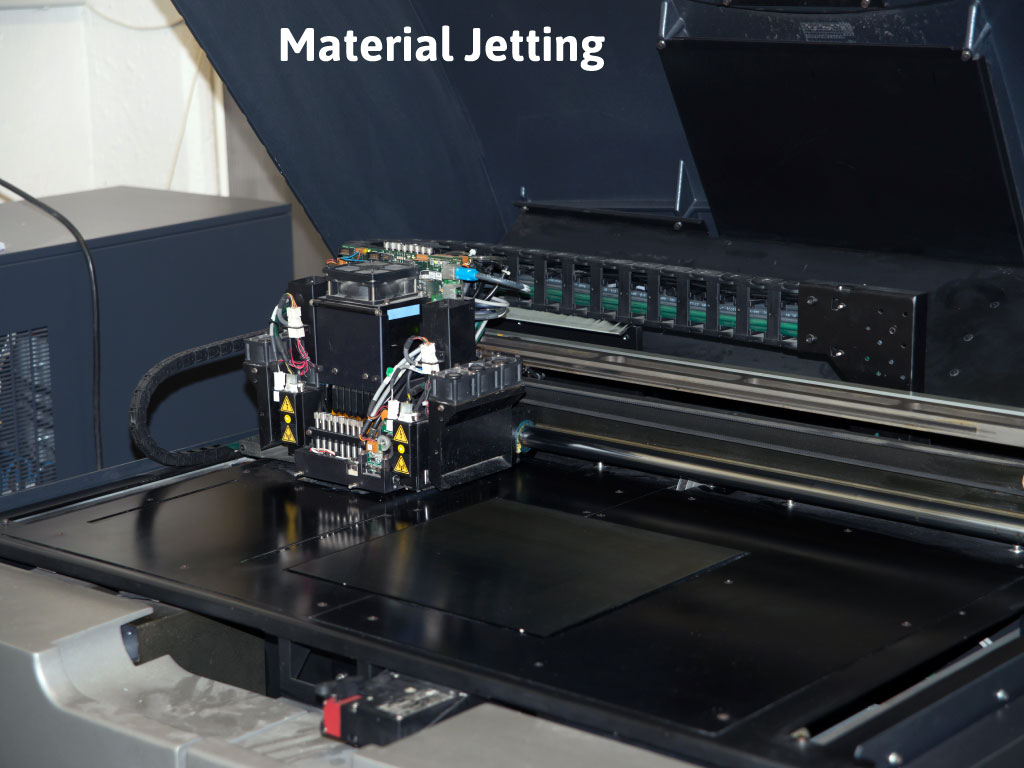
Selective deposition of liquid material in droplets followed by curing
Photopolymers
Polymers
Waxes
- Polyjet
- Projet
- Smooth Curvatures Printing

Sheets of material are stacked and laminated; unnecessary portions are selectively cut out
Paper
Plastic Sheets
Metal Foils
Tapes
- Laminated Object Manufacture
- Selective Deposition Lamination
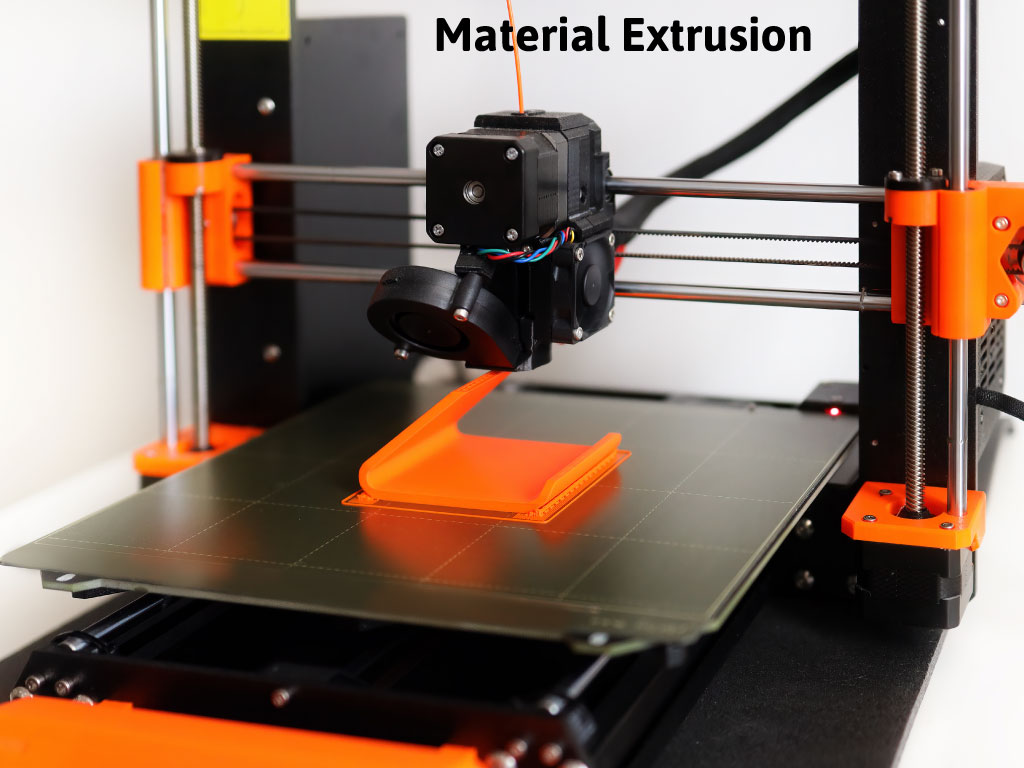
Selective deposition by extruding material through a nozzle
Thermoplastic Filaments and Pellets
Liquids
Slurries
- Fused Filament Fabrication
- Fused Deposition Modeling
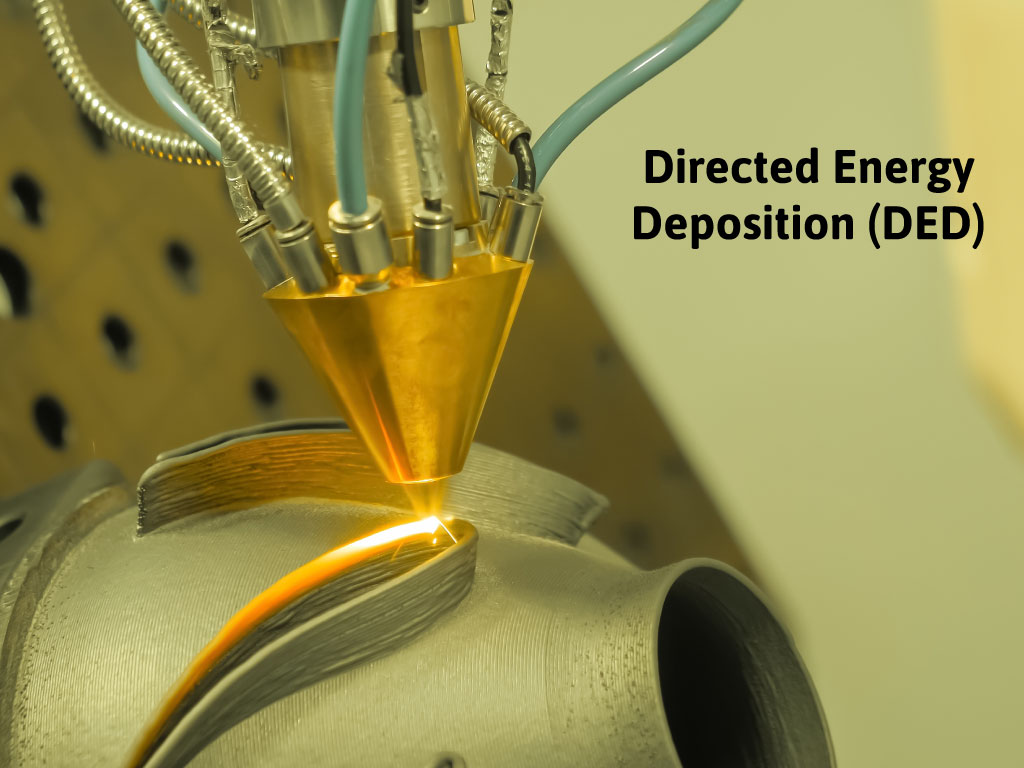
Selective deposition of metal on the surface and fusing it with underlying layers using an energy source
Metal Wire
Metal Powder
Ceramics
- Laser Metal Deposition
- Laser Engineered Net Shaping
- Direct Metal Deposition
- Laser Engineered Net Shaping
- Direct Metal Deposition
Source: Adapted from Additive Manufacturing4
Capabilities and Constraints of Additive Manufacturing
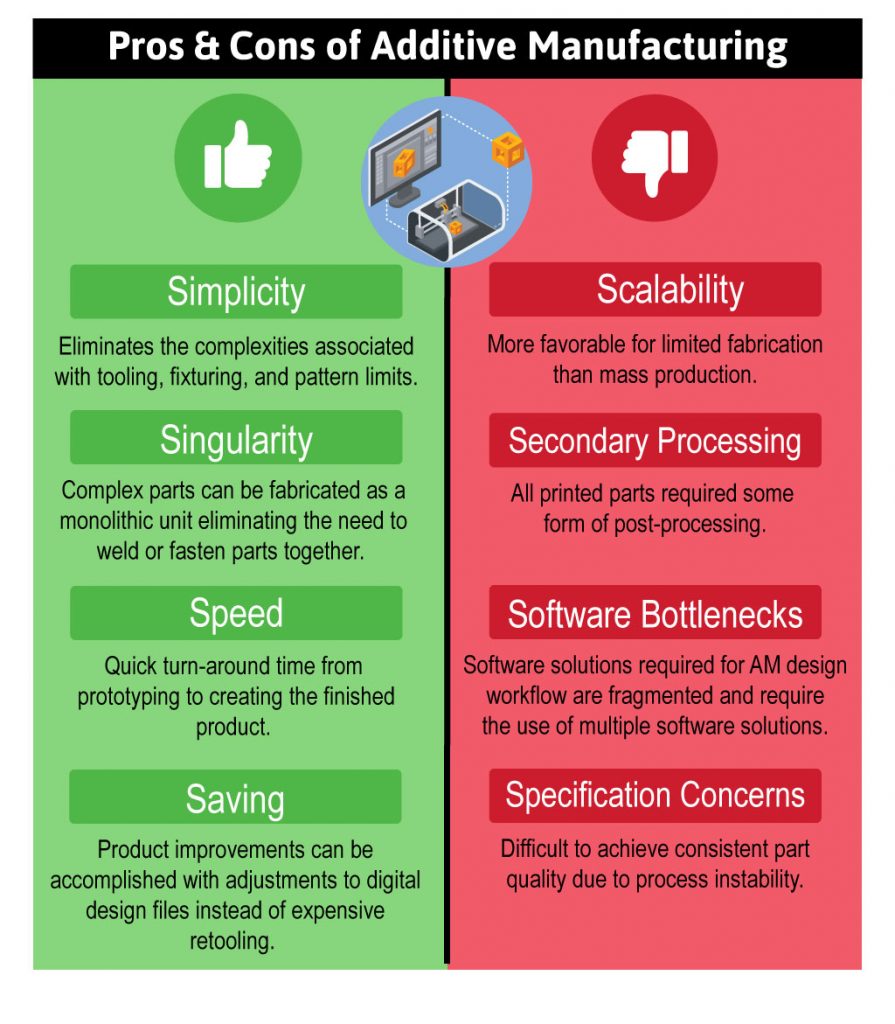
Despite all its challenges, 3D printing has gained wide acceptance by the professional community. Ongoing research in additive manufacturing promises to overcome current challenges and make it a mainstream industrial manufacturing process.
Predictions
According to an intelligence report published by Markets and Markets, the industry is estimated to grow from USD 9.9 billion in 2018 to USD 34.8 billion in 2024. This surge is largely driven by the demands of the healthcare sector. The mass production of personal protective equipment (PPE) during the public health crisis, COVID-19, has been a catalyst that propelled additive manufacturing to its mainstream status.
Additive manufacturing is poised to disrupt global supply chain models by virtue of shorter product development cycles. The ability to produce integrated features considerably reduces the need for multiple parts. Large multinational companies are researching the possibility of 3D printing their part5 for remanufacturing purposes.
Additive manufacturing is a robust technology in the manufacturing toolkit. Integrating additive manufacturing with subtractive methods will significantly enhance the capabilities of industrial manufacturing. Significant advances have been made in hybrid manufacturing technologies where printers are outfitted with machining platforms. Hybrid technologies harness the best of both worlds—the geometrical complexity achieved with additive manufacturing and the precision achieved with machining processes.
Conclusion
Whether you are continuing with subtractive technologies or are jumping on the additive bandwagon —THORS eLearning Solutions meets your learning and development needs in the manufacturing realm. Industry-vetted content with stunning visuals and interactives will flatten your learning curve. Explore our product offerings: standard courses, Lightning Learning, and custom courses. Interested in information on powder production for additive manufacturing? Check out our Powder Metallurgy Basics. Can’t find what you need? Talk to us. Our team can build it for you.
2Liquid Rules, Mark Miodownik, 2019, Houghton Mifflin Harcourt. pp. 200–202.