The Role of Technology and Automation
Combining automation with human expertise offers a promising solution to challenges posed by baby boomer retirements in manufacturing. While technology and automation can’t fully replace the nuanced understanding and experience of seasoned workers, they present significant potential to fill gaps and boost productivity. Yet, a careful balance of automation and human skills is essential to ensure the industry continues to thrive on innovation and quality.
Filling the Gaps with Technology
Advanced technologies such as robotics, artificial intelligence (AI), and machine learning are transforming manufacturing floors, taking over tasks that are repetitive, hazardous, or require precision beyond human capability. Automation can increase production efficiency, reduce errors, and maintain consistency in quality, directly addressing some of the productivity gaps that may arise with the departure of experienced workers. Furthermore, Internet of Things (IoT) devices and sensors provide real-time monitoring and data analytics, offering insights that can lead to more informed decision-making and predictive maintenance, minimizing downtime and extending the lifespan of machinery.
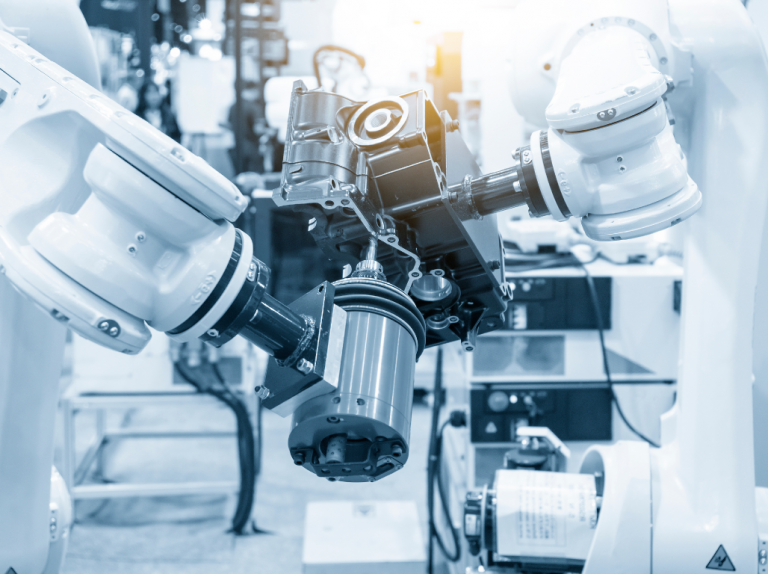
Balancing Automation with Human Expertise
Despite these advances, the value of human expertise cannot be understated. Critical thinking, problem-solving, and creative innovation are inherently human traits that technology cannot replicate. Thus, the focus should be on leveraging technology to augment human capabilities rather than replace them. Automation can free up workers from mundane tasks, allowing them to focus on areas that require human insight, such as strategic planning, design, and troubleshooting complex issues.
Manufacturers must strive to find the right balance between adopting new technologies and valuing their workforce’s knowledge and experience. Training programs that upskill workers to operate and interact with new technologies can help bridge this gap. By doing so, employees can transition from purely manual tasks to more cognitive roles, overseeing automation processes, analyzing data, and contributing to innovation.
Ensuring Technology Complements the Human Touch
The integration of technology in manufacturing should be designed to complement human work, creating a symbiotic relationship where each enhances the other’s strengths. For instance, collaborative robots, or “cobots,” are designed to work alongside humans, combining the precision and consistency of machines with the problem-solving capabilities and adaptability of humans. Such partnerships can lead to safer working environments, increased efficiency, and higher job satisfaction as workers engage in more meaningful and less hazardous tasks.
In summary, technology and automation offer powerful tools to address the workforce challenges posed by the retirement of baby boomers. However, the success of these technologies lies in their ability to complement human expertise, creating an integrated manufacturing environment that values both innovation and the irreplaceable human touch. This balanced approach will be crucial for the manufacturing sector to navigate the transition and capitalize on the opportunities presented by technological advancements.
Preparing for the Future
As the manufacturing sector continues to navigate the complexities of workforce transitions companies must look ahead and prepare for the future. Ensuring the workforce is resilient, adaptable, and capable of evolving with industry changes is not just beneficial but essential for long-term success and competitiveness. Here are some key recommendations for manufacturing companies aiming to future-proof their workforce.
Embrace Continuous Learning and Development
The pace of technological advancement and the evolving landscape of the manufacturing industry necessitate a commitment to continuous learning and development. Companies should invest in training programs that not only upskill employees on current technologies but also foster a culture of lifelong learning. This approach ensures that the workforce can adapt to new tools, processes, and methodologies as they emerge, keeping the company at the forefront of innovation.
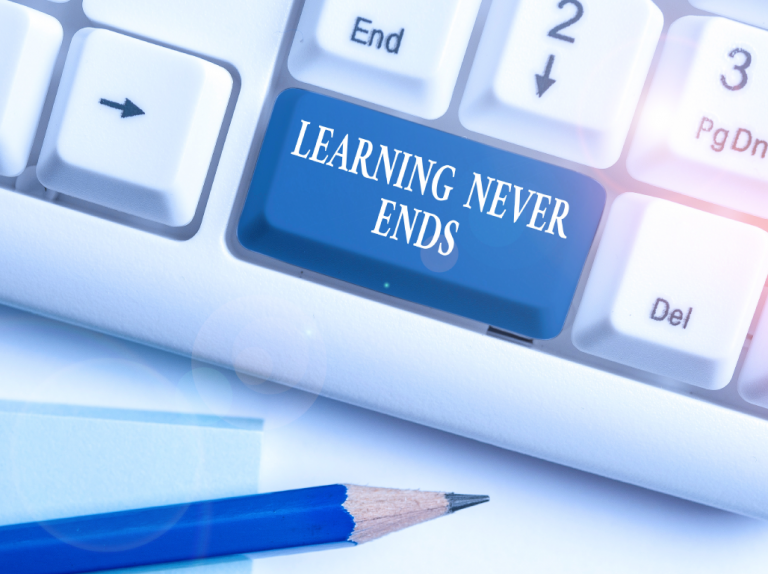
Foster Diversity and Inclusivity
Diversity in the workforce can drive innovation and creativity by bringing together varied perspectives, experiences, and problem-solving approaches. Encouraging inclusivity and diversity not only enhances the company’s culture but also widens the talent pool, making it easier to fill gaps and adapt to changes. Efforts to recruit from different demographics, including younger generations, women, and underrepresented groups, can infuse new energy and ideas into the manufacturing sector.
Leverage Technology for Talent Management
Advancements in HR technologies, including AI-driven analytics, can help companies better manage talent and predict workforce needs. These tools can identify skills gaps, forecast hiring needs, and even suggest career development paths for employees, enabling proactive workforce planning. By leveraging these technologies, companies can ensure they have the right talent in place to meet future demands.
Build Strategic Partnerships
Forming partnerships with educational institutions, technical schools, and industry associations can help companies stay ahead of workforce trends. These partnerships can facilitate internships, apprenticeships, and co-op programs that prepare students for careers in manufacturing, ensuring a steady pipeline of skilled workers. Moreover, collaboration with industry groups can provide insights into emerging trends and best practices for workforce development.
Prioritize Employee Engagement and Retention
Engaged employees are more likely to stay with a company, reducing turnover and the associated costs of recruiting and training new workers. Manufacturing companies should focus on building a positive work culture where employees feel valued, supported, and engaged. Recognition programs, career development opportunities, and open communication channels can all contribute to higher levels of employee satisfaction and loyalty.
Preparing for the future amidst the ongoing retirement of baby boomers and other workforce transitions requires a strategic, multifaceted approach. By focusing on continuous learning, diversity, technology, partnerships, flexibility, and engagement, manufacturing companies can build a workforce that is not only capable of meeting current challenges but also poised to drive future success. This proactive approach to workforce development will be key to navigating the changes that lie ahead and securing a prosperous future for the manufacturing sector.
Conclusion
The retirement of baby boomers from the manufacturing sector marks a significant turning point, presenting both challenges and opportunities for the industry. As this experienced workforce exits, they leave behind gaps in jobs and knowledge that need urgent attention. These gaps pose risks to production efficiency, safety, innovation, and the overall growth of the manufacturing sector. However, within these challenges lie opportunities for transformation and revitalization. By adopting strategic measures to attract younger workers, facilitate knowledge transfer, and integrate technology and automation, the manufacturing industry can navigate this transition successfully.
The call to action for industry leaders is clear: proactive measures must be taken to address the impending job and knowledge gaps. This includes modernizing the image of manufacturing to attract a new generation of workers, implementing comprehensive mentorship and training programs to capture and transfer the wealth of knowledge held by retiring employees, and leveraging technology to augment human capabilities rather than replace them. Additionally, fostering a culture of continuous learning and adaptability will ensure that the workforce remains resilient in the face of future changes.
As the manufacturing sector stands at this crossroads, the actions taken today will shape its future. It is an opportune time for industry leaders to rethink strategies, invest in their workforce, and embrace innovation. By doing so, they can ensure that the manufacturing industry not only survives this period of transition but thrives, continuing to grow and compete on a global stage. The retirement of baby boomers is not just a challenge to overcome but a catalyst for renewal, pushing the industry toward a more dynamic, inclusive, and innovative future.
Hope you enjoyed this three-part blog! Click here if you missed part 1 or part 2.