Course Description
The Cupola Furnace Troubleshooting and Techniques course is an informative advance-level course for cupola operators working firsthand with a cupola furnace. The course provides operators with an introduction to the most common troubleshooting situations and practical techniques to employ when problems occur. It also focuses on the ramifications of cupola design, the benefits of operating an optimally designed cupola, as well as how to make desired changes to carbon content, spout temperature, and melt rate.
Who will benefit from this Cupola Furnace Troubleshooting course?
Cupola operators, cupola foremen, melt superintendents.
Course Classification
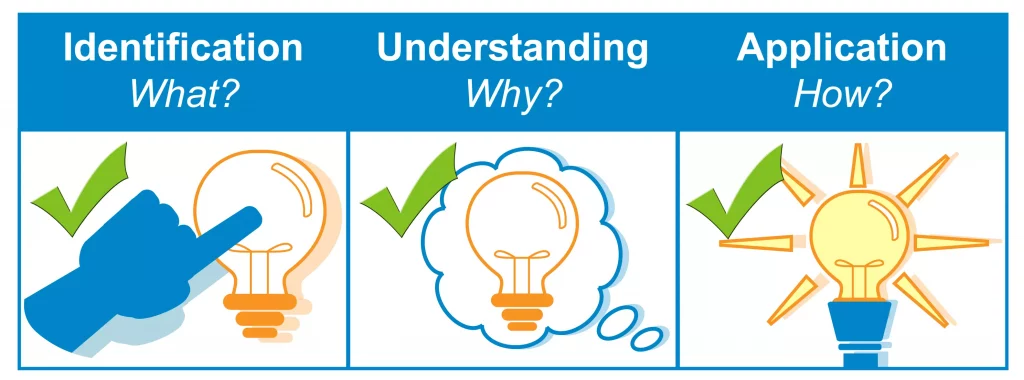
*THORS uses the Bloom’s Taxonomy Methodology for our course development.
Certificate Awarded for Cupola Furnace Troubleshooting and Techniques

*upon successful completion
Related Posts

Green Sand: A Classic Casting Recipe
Casting Chronicles The history of humanity is defined by man’s relationship with the material world. Man’s ability to make tools from metals has changed our
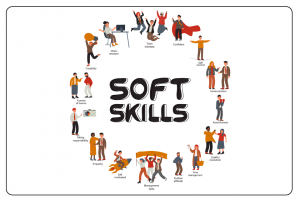
Developing Soft Skills in the Tech Industry
Soft skills in the tech industry, where precision and expertise are paramount, might seem secondary. However, soft skills such as communication, teamwork, and problem-solving, play
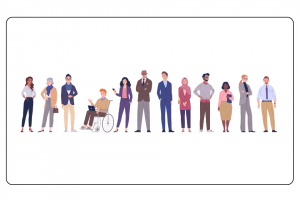
Cross-Cultural Training Benefits
Understanding Cross-Cultural Training In today’s interconnected world, businesses are expanding beyond borders. To thrive globally, organizations must equip their employees with cross-cultural skills. Cross-cultural training