Advanced Product Quality Planning (APQP) helps an organization with effective cost and time management by dividing a product development process into the five phases of APQP. Here is an overview of the five phases of APQP and their relevance as a project management tool.
What is APQP?
Advanced Product Quality Planning (APQP) is a project management tool to develop and produce products that meet customer requirements through meticulous planning and error prevention. This is achieved by dividing the product development process into the five phases of APQP and then further dividing the phases into activities to micromanage the process.
What are the Phases of APQP?
APQP Phase 1
Phase 1 in APQP, also known as plan and define program, focuses on the customer needs and expectations. The multidisciplinary team plans the activities of the first phase of APQP with the customer in mind. The experience and knowledge of the team helps minimize errors and ensures that even minute details are not missed.
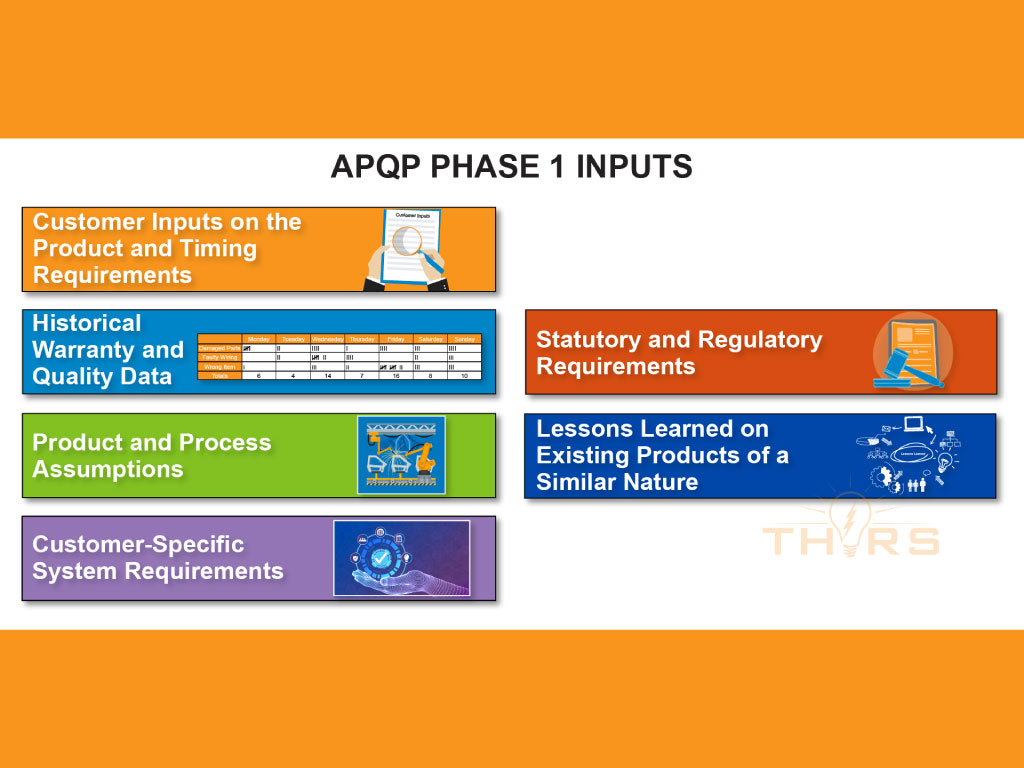
The outputs of APQP Phase 1 are the following:
- Product development timing plan
- Design goals
- Reliability and quality goals
- Preliminary bill of materials
- Preliminary process flowchart
- Management approval and support
APQP Phase 2
Phase 2 in APQP is the product design and development phase. In the second phase of APQP, the design goals, reliability goals, and quality goals that were developed in the planning phase are given a near-final shape. This phase will not be applicable to organizations that manufacture products as per the designs provided by the customers. This phase is applicable only if the manufacturing organization is responsible for the product design.
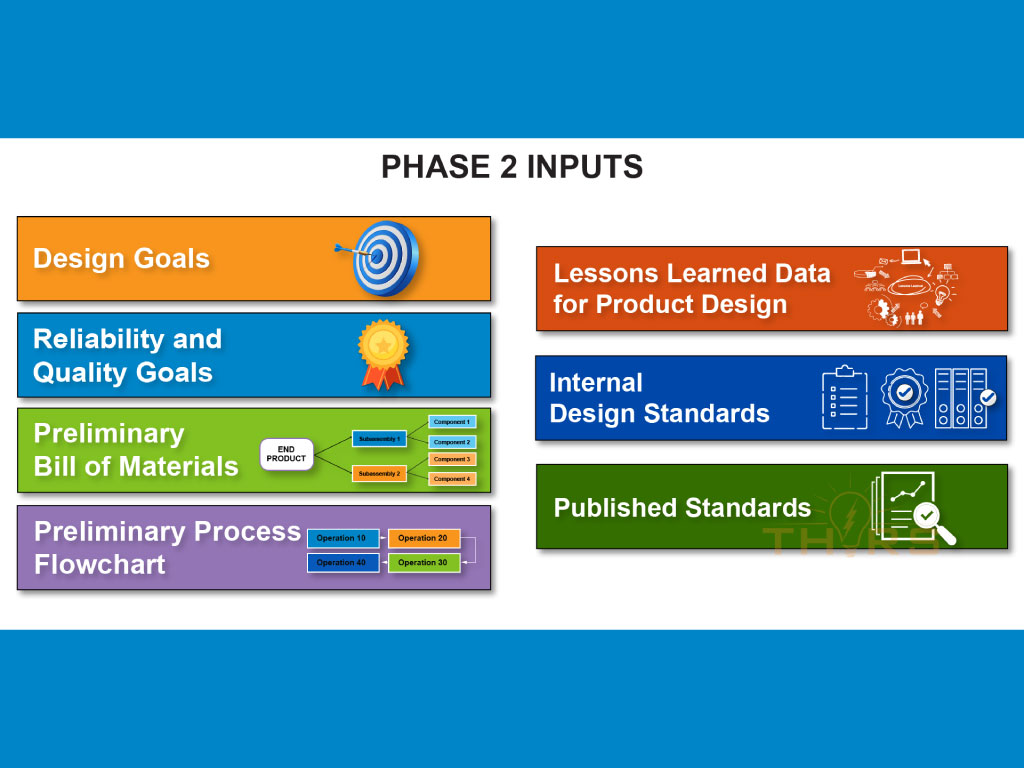
The outputs of APQP Phase 2 are the following:
- Bill of materials
- Product drawings, materials, and test specifications
- Design Failure Mode and Effects Analysis (DFMEA)
- Design verification
- Design review
- Prototype control plan
- New equipment, tooling, and facility requirements
- Gauge and test equipment required
- Finalization of special characteristics
- Team feasibility commitment and management support
APQP Phase 3
Phase 3 in APQP is called process design and development. In the third phase of APQP, the focus is to ensure the comprehensive development of an effective manufacturing system.
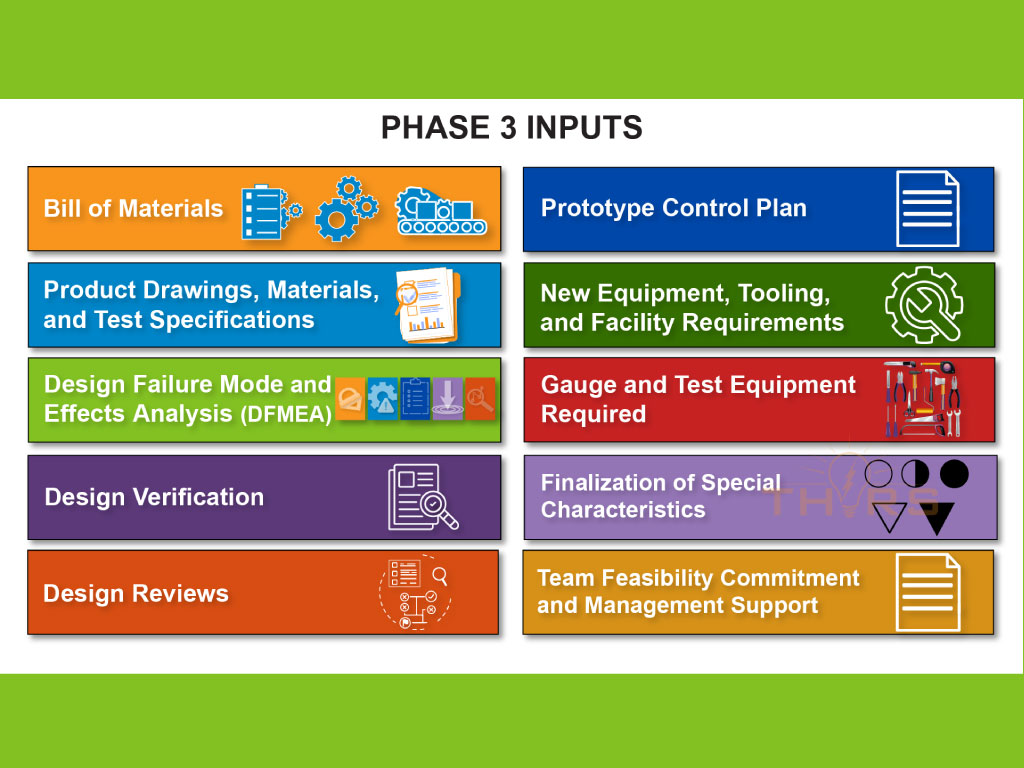
The outputs of APQP Phase 3 are the following:
- Packaging standards and specifications
- Process Flow Diagram (PFD)
- Process Failure Mode and Effects Analysis (PFMEA)
- Pre-launch control plan
- Workstation instructions
- Measurement System Analysis (MSA) study plan
- Preliminary process capability study plan
- Tool and gauge design drawings
- Purchasing inquiries and ordering of tooling, gauges, and raw material
- Management support
APQP Phase 4
Phase 4 in APQP is product and process validation. In the fourth phase of APQP, the customer validates the product and the manufacturing process. During the significant production run, the multidisciplinary team should ensure that the process control documents, such as the Process Flow Diagram (PFD), Process Failure Mode and Effects Analysis (PFMEA), Control Plan, and Operator Instructions are being followed.
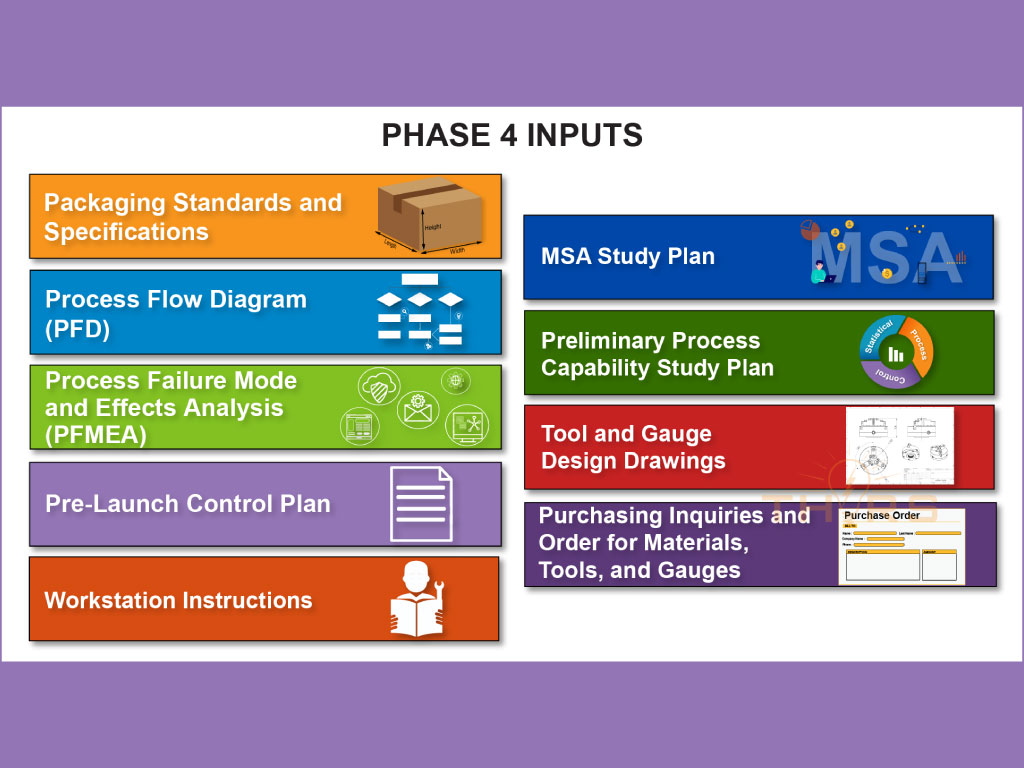
The outputs of APQP Phase 4 are the following:
- Significant production run
- Measurement System Analysis (MSA) study results
- Preliminary process capability study results
- Product approval and validation by customer
- Production control plan
- Packaging evaluation
- Quality planning sign-off and management support
APQP Phase 5
Phase 5 in APQP is called feedback, assessment, and corrective action. The feedback, assessment, and corrective action phase is the only phase that runs from start to finish of the program and illustrates the need to apply corrective actions and course corrections throughout the program to ensure the on-time delivery of a quality product. The fifth phase of APQP continues until the bulk supply has been streamlined after the resolution of all concerns. The team needs to update the lessons learned database and then close the APQP program.
APQP Phase 5 assumes greater importance at the product manufacturing stage, or APQP Phase 4, where the outputs can be evaluated for the effectiveness of the quality planning effort. Countermeasures must be deployed promptly for any concerns raised during evaluation. In APQP Phase 5, the inputs can vary based on the concerns encountered in each phase.
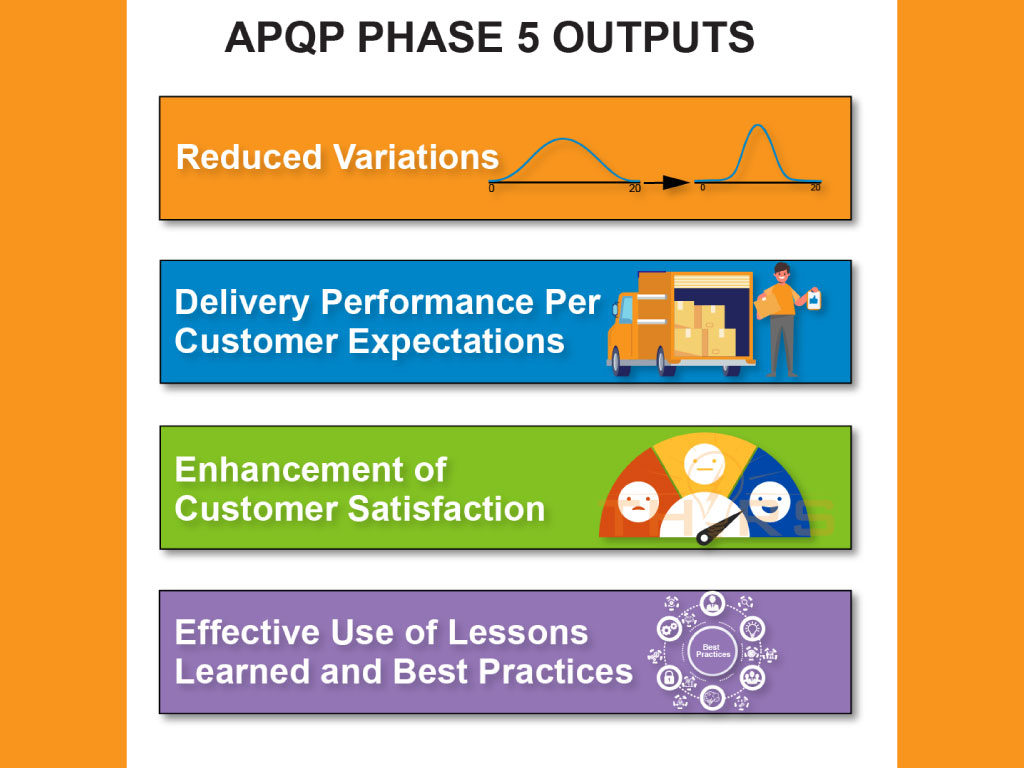
What is the Relevance of APQP?
APQP facilitates communication and control among everyone involved in the product development process to ensure that all required steps are completed on time and at a cost that represents value.
Learn more about Advanced Product Quality Planning and the phases of APQP in the visually engaging and highly interactive THORS course.