Course Description
Bonded Sand Fundamentals is an introduction to bonded sand molding processes, including the mold and core preparation, pouring, solidification, and separation of metal parts. Presented in THORS’ highly visual and interactive learning format, this course will help foundry employees become familiar with the important equipment and terminology associated with their profession.
Who will benefit from this Bonded Sand course?
Companies, individuals, or educational institutions that produce castings from bonded sand molds.
Course Classification
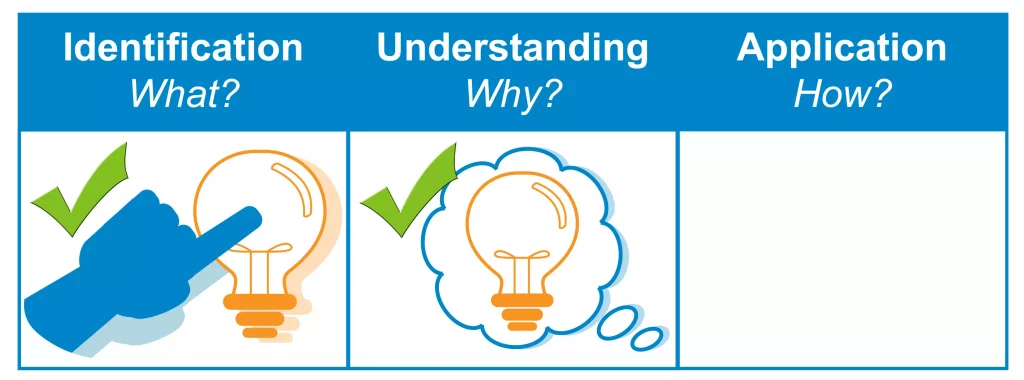
*THORS uses the Bloom’s Taxonomy Methodology for our course development.
Certificate Awarded for Bonded Sand Fundamentals

*upon successful completion
Related Posts

How Can THORS Help Enhance Your College Education?
THORS Academy can help enhance your college education in a number of ways. Imagine being in a college class and being told you have a
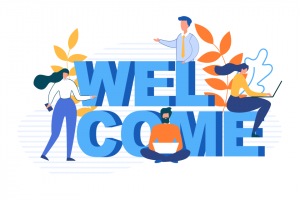
Orientation versus Onboarding: Understanding the Differences
When discussing “orientation versus onboarding”, it’s vital to recognize that, though frequently conflated, they serve distinct purposes in the professional environment. Despite both focusing on
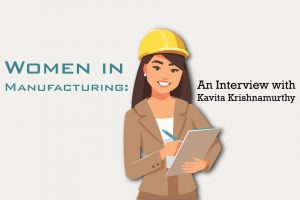
Women in Manufacturing: An Interview with Kavita Krishnamurthy
As part of a tribute to women in manufacturing, we at THORS eLearning Solutions decided to showcase one of our own, Kavita Krishnamurthy. Kavita is