Course Description
Polymers: Injection Molding Troubleshooting is an informative, advanced-level course on troubleshooting molded part defects created during the injection molding process. In this course, learners are introduced to the main problem areas that may affect molded parts during the injection molding process, including the mold, machine, material, and process. The course then discusses potential troubleshooting strategies, followed by a discussion of the most common defects that may affect a molded part. Learners in quality, manufacturing, sales or related, and research and development in the industry will find value in this course.
Who will benefit from this Injection Molding Troubleshooting course?
R&D new hires, manufacturing process engineers, sales reps – technical sales, account managers, product developers, tech service, product managers, quality managers.
Course Classification
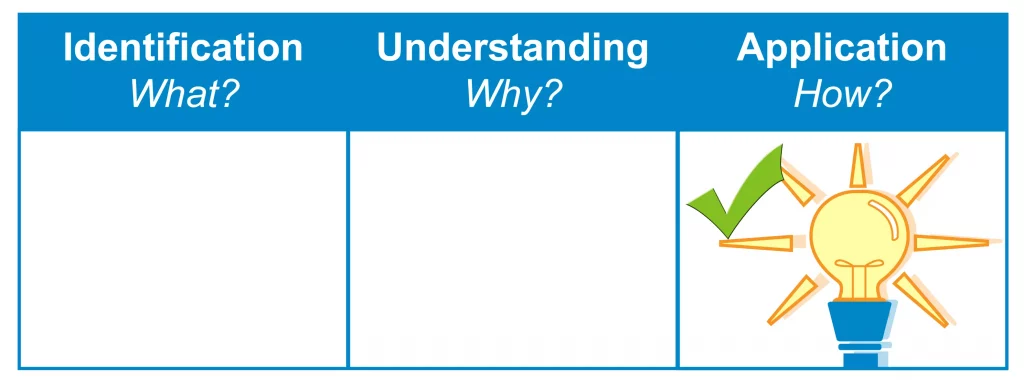
*THORS uses the Bloom’s Taxonomy Methodology for our course development.
Certificate Awarded for Polymers: Injection Molding Troubleshooting

*upon successful completion
Related Posts
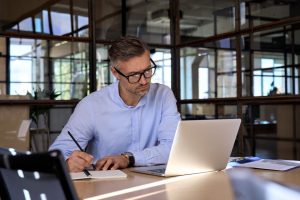
eLearning Support for On-Site Training
eLearning has emerged as a revolutionary force in the realm of learning and professional development, evolving into an imperative tool in today’s competitive landscape. The

5 Ways to Reduce Human Errors in Manufacturing
We cannot change the human condition, but in manufacturing we can certainly improve the way people work, where they work, and what systems they use.
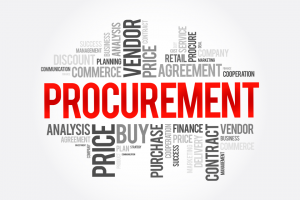
The Essential Skills of Modern Purchasing Professionals
In my professional career that spans more than three decades, I have had the privilege of working closely with purchasing. I can attest to the