What are Horizontal Machining Centers?
Horizontal machining center (HMC) safety involves machines that have spindles oriented horizontally, meaning that the cutting tools of the machine move parallel to the ground. Safety procedures and standard operating procedures are required to ensure the safety of employees, to improve productivity, and to maximize machine tool life. Workplace safety standards are set by the Occupational Safety and Health Administration, or OSHA. It is each employee’s responsibility to follow OSHA standards to ensure that the proper Personal Protective Equipment, or PPE, is always worn.
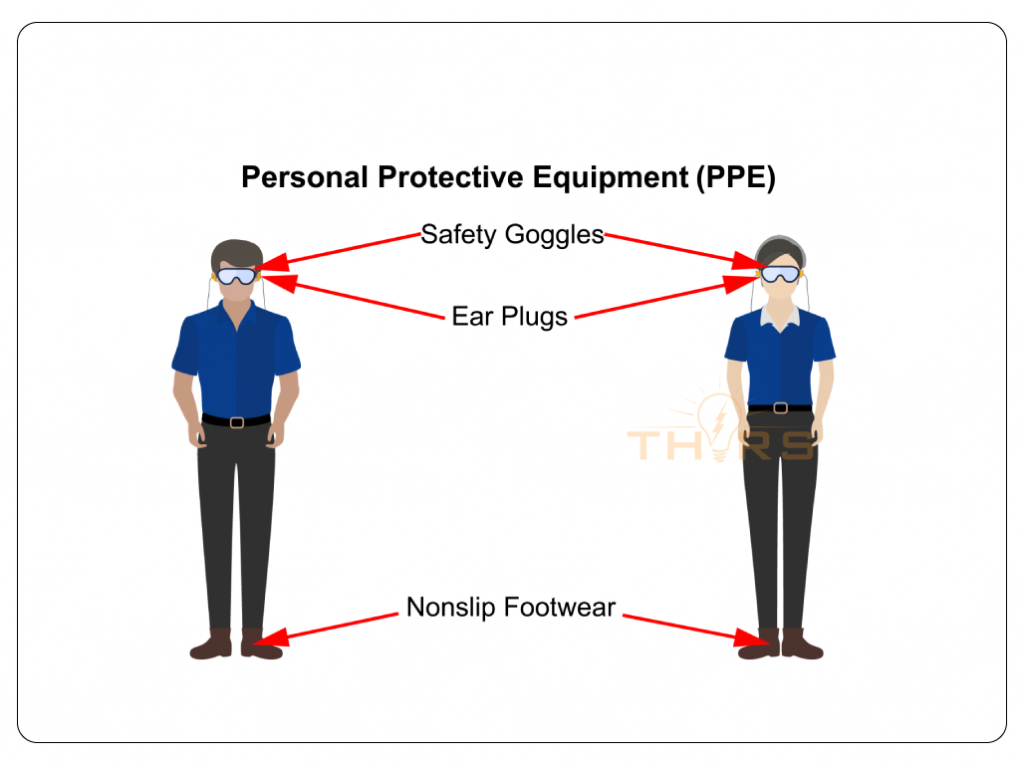
What is Horizontal Machining Center Mechanical Safety?
HMC operators must be aware of hazards that can be considered mechanical, such as the working components of the machine. Prior to approaching a machine, or opening any access panel, if applicable, operators must ensure that the machine is turned off and not capable of moving. Above all, operators are encouraged to pay close attention to and focus on the tasks required for their stations, with an emphasis on safety for themselves and others.
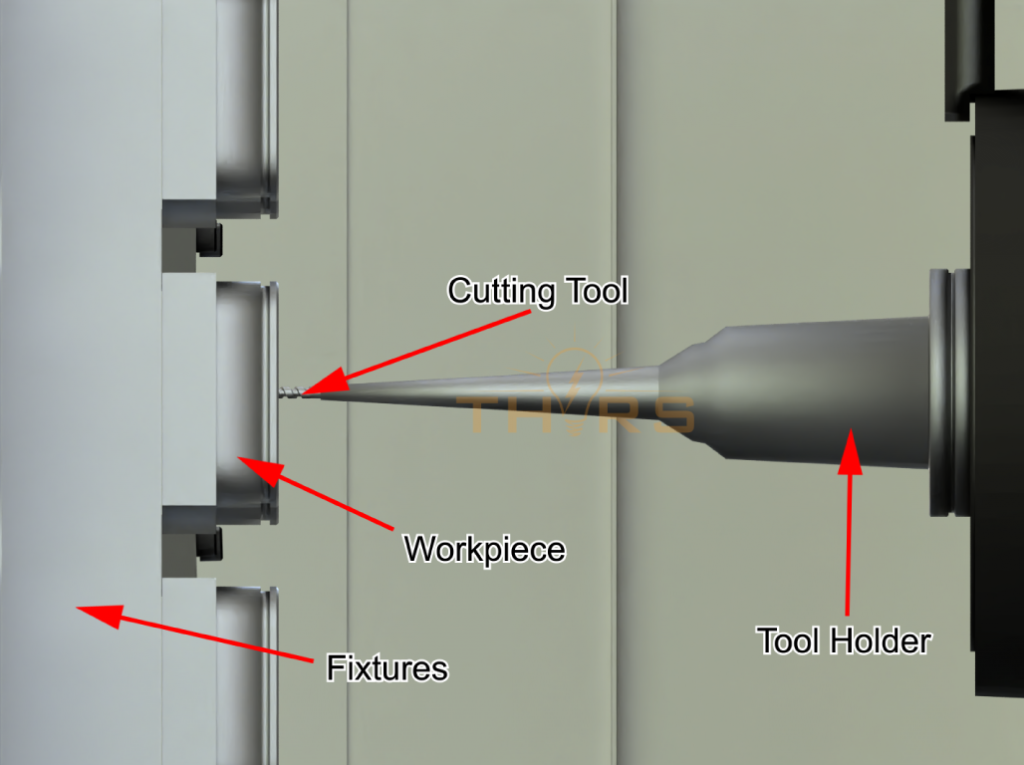
What is Horizontal Machining Center Liquid Safety?
Horizontal machining center safety requires that machine operators are aware of a variety of hazards that are related to liquids, involving either the coolant, cutting fluid, or lubrication systems of the machine. It is important to prevent the coolant from becoming contaminated during the machining process. Dust and other particles are always potential contaminants. Materials such as chips and swarf can end up in the coolant from machining, which can be prevented by ensuring that drum filters, V-seals, and screens are in place and functional.
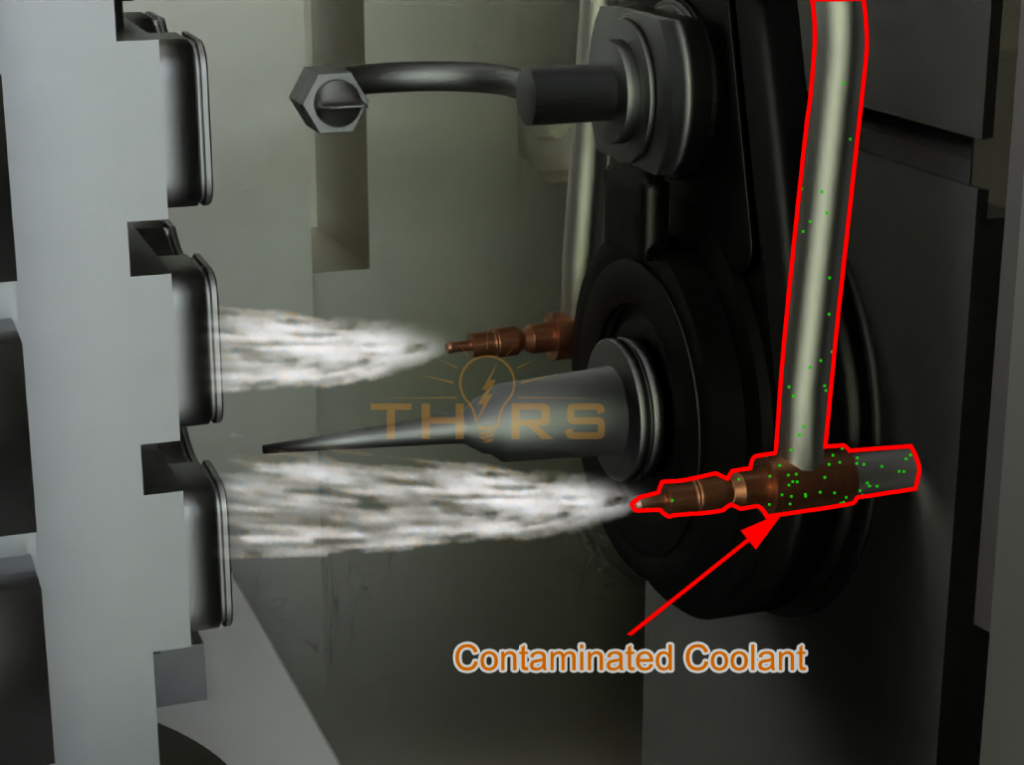
What is Horizontal Machining Center Electrical Safety?
Horizontal machining center safety requires that machine operators are aware of a variety of electrical hazards, or those related to the electrical systems of the machine. Operators should pay attention to advisory stickers, confined space restrictions, and other warning labels or required procedures, such as Lockout-Tagout, or LOTO. It must be ensured that the back door of the machine is closed before proceeding with the next job. The location of the nearest Emergency Stop, or E-Stop, button should be noted ahead of time so that an immediate shutdown of the machine can be performed if required. When working with electrical components, it is crucial to examine any areas prior to placing hands or fingers in the vicinity. Also, it should never be assumed that equipment is turned off and operators should always test electrical components before touching.
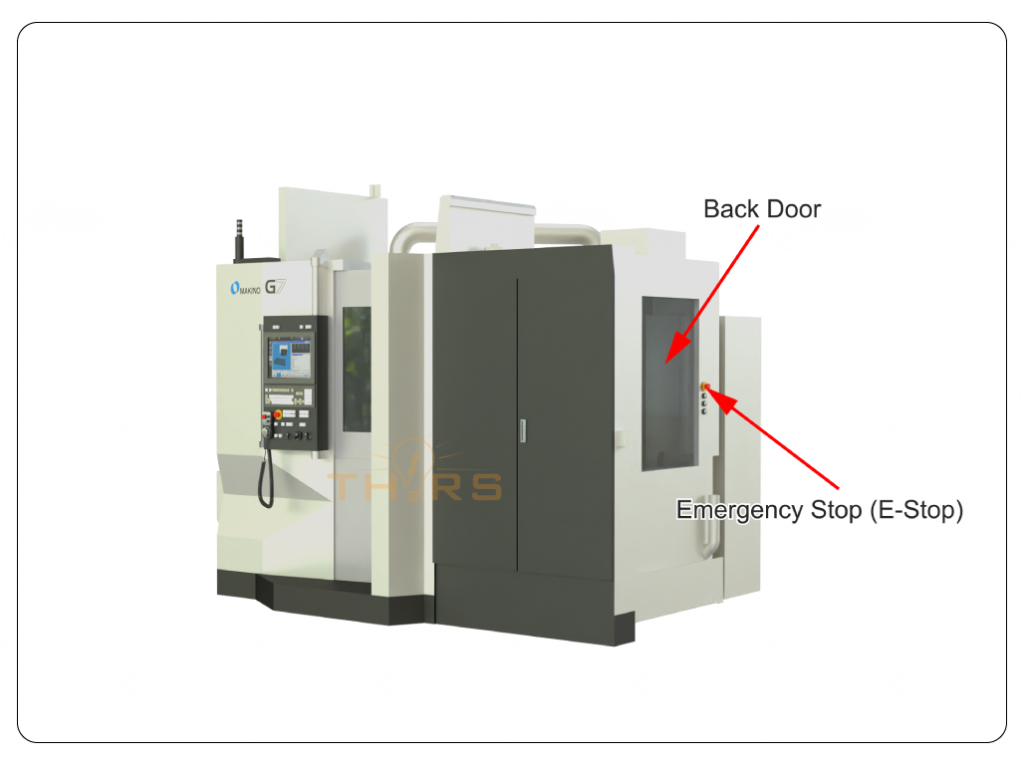
Machining operators must always be aware of safety standards and procedures put forth by their organization, particularly for the mechanical, liquid, and electrical aspects of the machines. However, operators must also be aware of many other variables such as the liquid pressure of the machine, the voltage ranges required, and the machine safety bypass feature of modern machines.
THORS presents the important aspects of horizontal machining center safety in our visual and interactive learning format. In addition, we have a diverse manufacturing excellence library covering a variety of safety, performance, and process improvement courses for manufacturing processes. Visit thors.com to expand the knowledge and skillsets of your workforce, and to ensure that your company has the highest quality training available today.