Chatter marks in centerless grinding pose a significant concern due to the process’s continuous and high precision nature, where even minor instabilities can lead to surface defects. Chatter marks are surface imperfections appearing as wave-like or rippled patterns on workpieces during grinding. These marks adversely affect surface finish, dimensional accuracy, and overall manufacturing efficiency. Eliminating chatter marks is essential for producing high quality parts and maintaining productivity.
The following are the most common causes of chatter marks in centerless grinding, along with recommended solutions to help minimize or eliminate their effects.
Machine Vibration
Mechanical vibrations originating from the grinding machine cause the grinding wheel and workpiece to oscillate relative to each other, leading to inconsistent material removal that results in chatter marks on the workpiece surface. These vibrations may result from loose or damaged components, insufficient machine rigidity, or external disturbances such as vibration transmitted from adjacent equipment.
Solutions:
- Implement a regular preventive maintenance schedule to inspect and replace worn spindle bearings, drive belts, and other mechanical parts.
- Tighten all fasteners and mounting points to ensure structural rigidity.
- Use vibration-dampening mounts or pads under the machine base to isolate it from floor or nearby machinery vibrations .
Grinding and Regulating Wheel Imbalance
Both the grinding wheel and the regulating wheel must be properly balanced to prevent vibration during centerless grinding. The grinding wheel runs at a very high speed, and so even a small imbalance can cause strong vibrations and lead to chatter marks. Although the regulating wheel rotates much more slowly, it controls how the workpiece turns and feeds through the machine. If the regulating wheel is unbalanced, it can cause the workpiece to rotate unevenly, resulting in chatter marks.
Solutions:
- Dynamically balance both grinding and regulating wheels prior to mounting.
- Balance the wheels again after dressing or when wheel conditions change significantly.
- Regularly inspect wheels for damage such as cracks, chips, or uneven wear, which can disrupt balance.
- Utilize balancing flanges or specialized balancing machines to achieve precision balance.
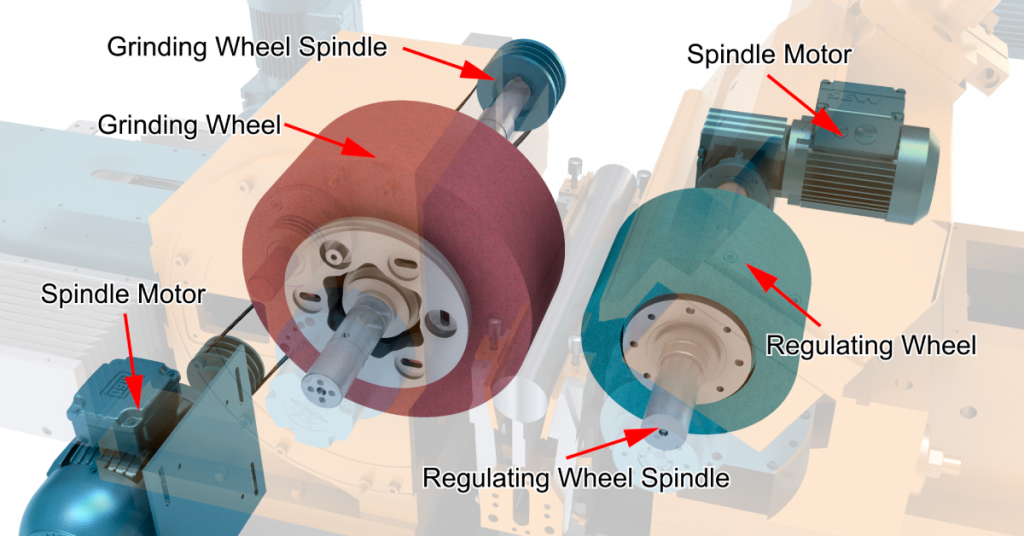
Improper Wheel Dressing
Dressing restores the grinding wheel’s shape and surface condition. Incorrect dressing parameters such as improper dressing speed or the use of worn dressing tools, can create uneven patterns or irregularities on the grinding wheel surface. These surface variations are then transferred to the workpiece during grinding, resulting in chatter marks.
Solutions:
- Use sharp, properly aligned dressing tools such as single-point diamonds or rotary dressers.
- Maintain consistent and appropriate dressing speeds and traverse rates for the wheel material and size.
- Finish dressing with a light pass to smooth out the wheel surface before grinding.
- Periodically check and replace worn dressing tools to ensure consistent performance.
Worn or Damaged Workblade
The workblade provides crucial support to the workpiece during the grinding process, maintaining its position and stability. Over time, due to continuous contact and wear, the blade can become worn, chipped, or deformed, which results in uneven or inconsistent support. This can cause the workpiece to shift or vibrate during grinding, contributing to chatter marks.
Solutions:
- Inspect the blade regularly for wear or flattening.
- Select blade materials suitable for the workpiece and grinding conditions.
- Maintain cleanliness around the blade to prevent build-up of debris that could alter support.
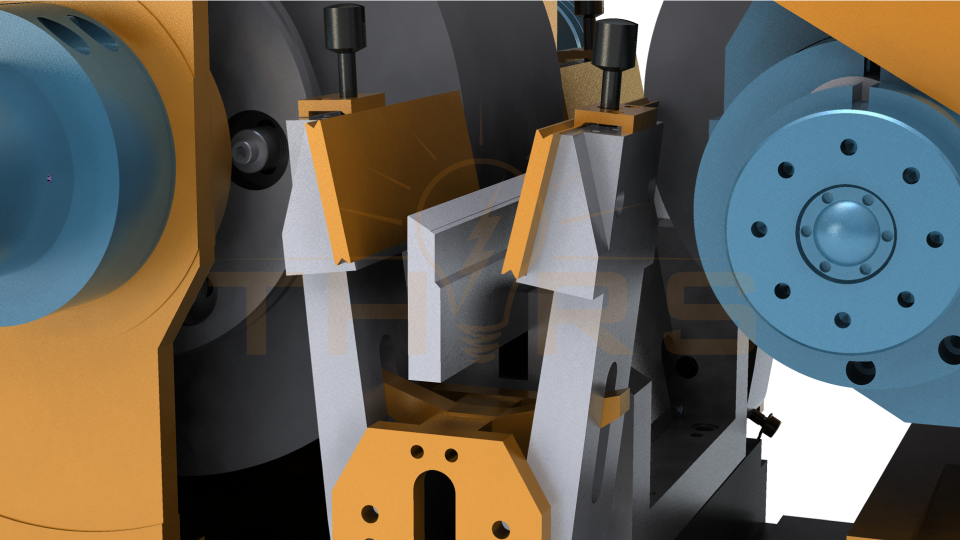
Conclusion
By understanding and addressing these specific causes, manufacturers can effectively minimize chatter marks in centerless grinding. Reducing chatter marks leads to improved surface finish, dimensional precision, and overall process reliability. Chatter often arises from issues related to machine setup and parameter selection. A solid understanding of grinding and dressing parameters, as well as proper machine setup is essential for achieving stable and high quality centerless grinding.
To learn more, check out our course here.
Want to find out how to launch this course and others to your team or organization? Contact us today!