Many have called metrology a necessary evil, but today metrology is appreciated for its indispensable role in adding value to the production line. In manufacturing, a good part of it comes down to performance and safety, which is enhanced by incorporating metrology in the manufacturing process. Metrology sheds light on how much a manufactured part has adhered to the intended specifications.
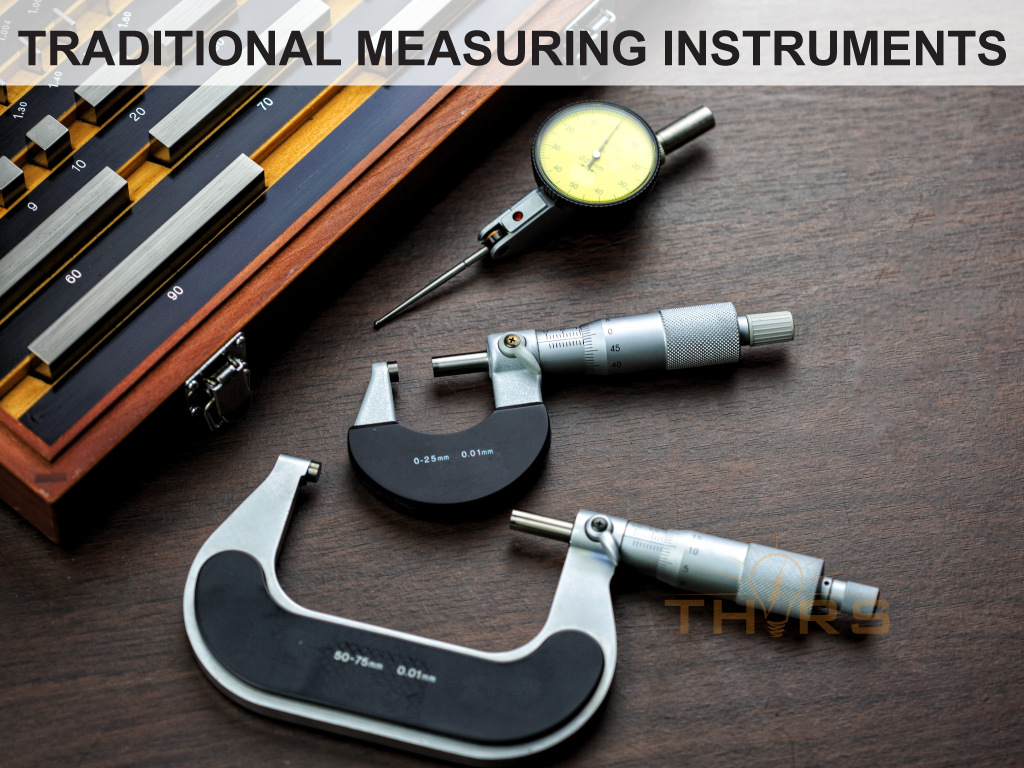
What instruments demand a skilled operator?
Traditional precision measuring instruments, such as gauges, calipers, and micrometers demand a skilled operator. The time-consuming process was not very accurate. The need for quick and precise measurement, combined with technological evolution in the 1960s, led to the remarkable inception of the Coordinate Measuring Machine (CMM). Since then, CMMs have never fallen out of trend but have been constantly revolutionized to widen their potential . The estimated market size of CMM by 2026 is $4.3 billion USD according to MarketResearch.com report SE 6753, published in July 2021. This piece of technology is deployed by automotive, aerospace, and many other industries to cut down on time and cost, and to deliver high quality parts and systems.
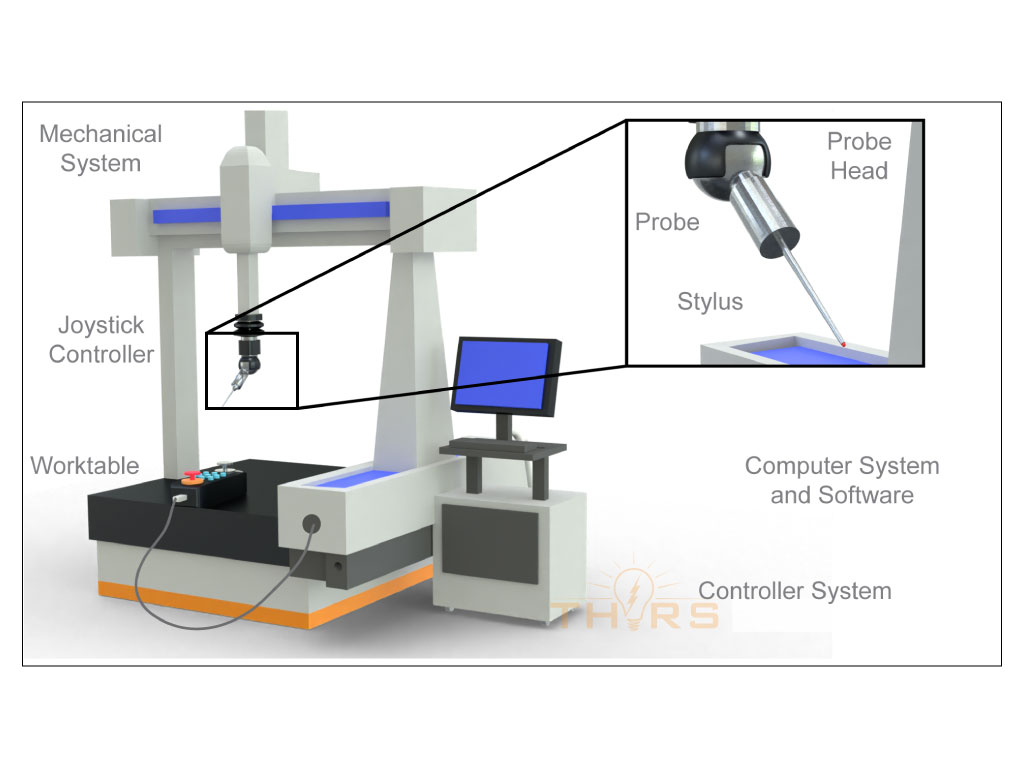
When is a CMM brought into play?
Any dimensional and geometrical errors can open the door to a myriad of problems in the production line. It is here that a CMM is used to inspect parts for the correctness of form and geometry. There is no need to fret about assembly, as CMMs provide data on fitting and pairing parameters. The huge volume of data generated for a part can be utilized for numerous analyses. At any point in time, the data can be stored, shared, and retrieved. CMMs have outwitted the traditional forms of measurement, in that a single machine does multiple measurement tasks.
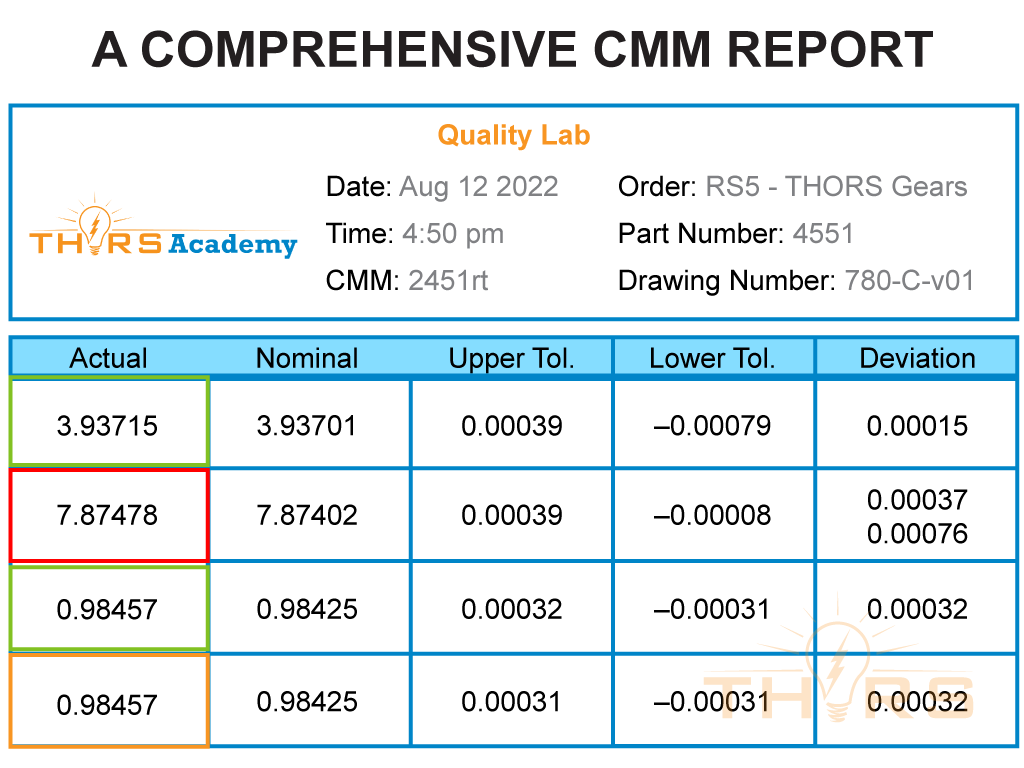
What is the measuring methodology?
A CMM does all measurements by using the coordinates of points collected on a part. A CMM using the stylus touches distinct points on the part and maps out the size, shape, and dimension of the part. It works similarly to connecting the dots with a pencil to form a picture. Each point has three values along the X, Y, and Z axes, which will help the CMM locate the point on the part.
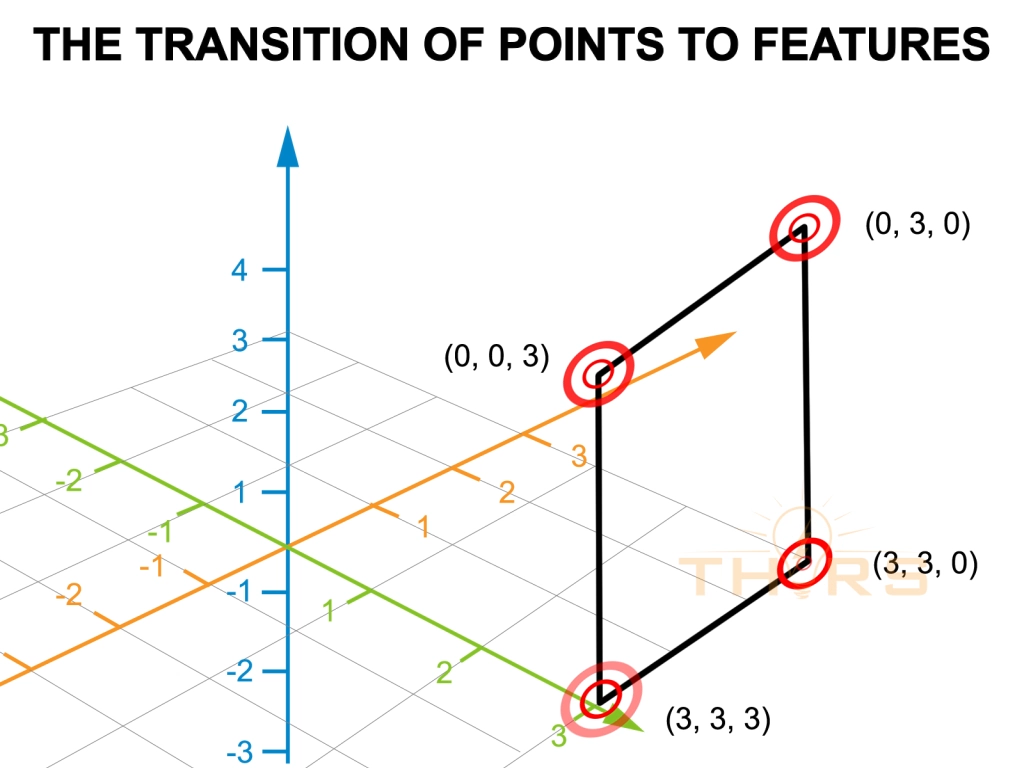
The three values are the coordinates of a point. Likewise, the coordinates of hundreds of points are captured by the CMM to further compute the many measurements demanded by the part. Measurements done through a CMM do not alter the part; therefore, the part is good to go after inspection, provided that all the measurement requirements are met.
A CMM is primarily used to measure the geometrical features and characteristics of a component. A software-driven CMM, in most cases, needs no intervention by an operator during the measurement process. The measurement happens by mounting the part on the machine with the help of fixtures. The CMM acquires measurement data through a mechanical process called probing.
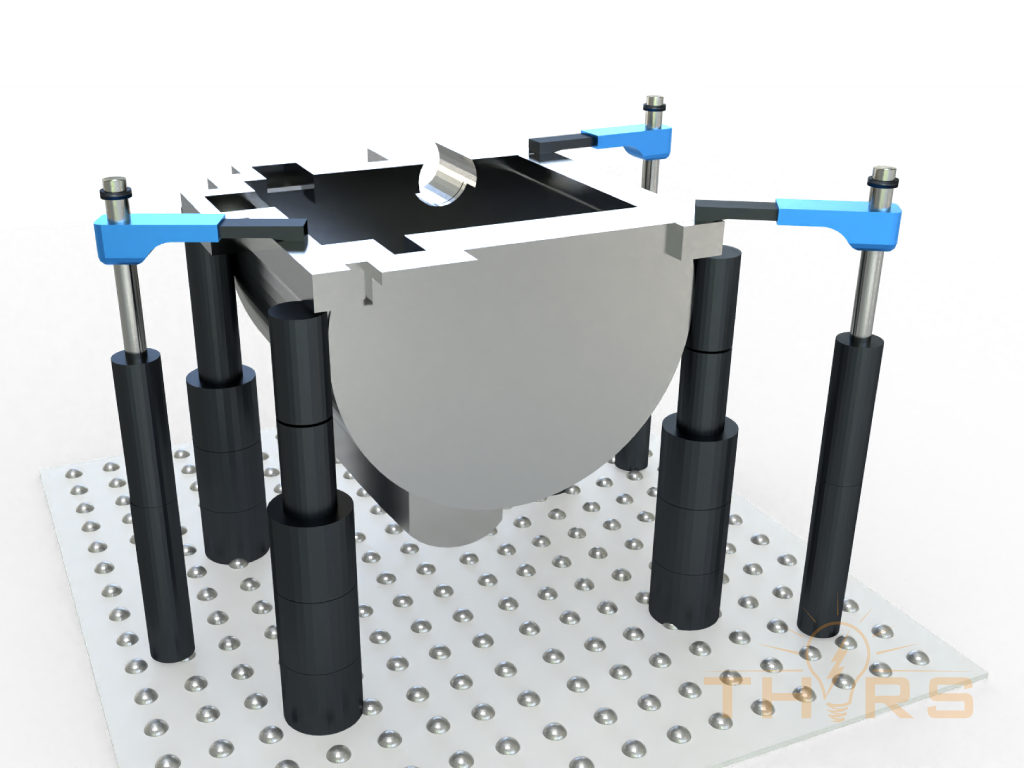
Probing is carried out by a probe that moves along the X, Y, and Z axes in addition to the rotary axes. Probing involves both contact and noncontact methods, which both require training. A contact probing method acquires data by contacting the part, while a noncontact probing method uses a laser beam and a camera to obtain data remotely. The software analyzes the data to map out the features of the object.
Who should handle a CMM?
Software and programming widen the usability of CMMs and do not demand high technical knowledge to perform measurements. However, there’s no getting around the fact that some basic skills are required to operate a CMM. A few of them are listed below:
- Computer operation skills
- Basic math skills
- Fundamental knowledge of measurement
- Manufacturing industry experience
- Good understanding of Geometric Dimensioning and Tolerancing (GD&T)
- Comprehensive understanding of Computer-Aided Design (CAD)
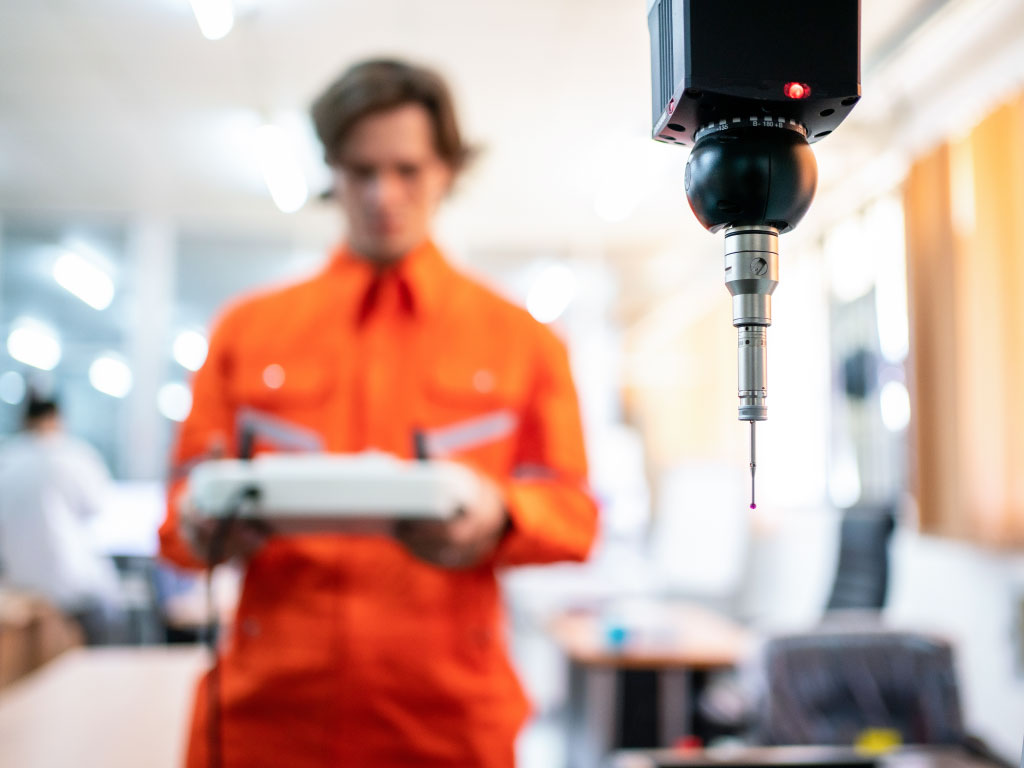
Why are CMMs so popular?
CMMs have proven advantages in the manufacturing process and have become a manufacturer’s friend. CMMs enable one setup for almost all measurement needs, involve less operator influence, provide accurate readings, and allow for the measurement of a wide range of components. Anything from a simple sphere to a big truck door can be measured by a CMM. In addition, a CMM measures the surface finish of a part as well as takes care of the GD&T requirements for an assembly.
Avoiding manufacturing errors before reaching the final stage of production increases productivity as well as reliability. A CMM brings a manufacturer one step closer to delivering high quality and perfectly fitting parts.
In the field of metrology, a CMM is one of the most celebrated measuring machines. Having understood the indispensable role of CMMs in the world of metrology, the THORS course on Coordinate Measuring Machine (CMM) Basics introduces the learner to the types of CMMs, the components, the measuring methodology, and the measurement analysis methods employed.