Sustainability in the production of engine valves, like many other automotive components, has become increasingly important in the face of climate change and resource depletion. However, these discussions often hit a dead end when considering how to maintain efficiency while pursuing sustainability. Are sustainability and performance truly at odds with each other? Not necessarily. This article explores how sustainability can be achieved in engine valve manufacturing without compromising the efficiency and functionality.
Material Selection
Steel is the predominant material used in manufacturing engine valves due to its superior physical properties, such as strength and corrosion resistance. However, this choice is not particularly eco-friendly. Nevertheless, various sustainable alternatives have been researched to find a solution. Recently, composite materials have emerged as a potential alternative. A study on composites argues that besides promoting reduced fuel consumption and eco-friendliness, composites offer perks like light weight, high strength, wear resistance, and excellent fire and lightning protection. Although research on composites is still in its nascent stages, it presents an efficient alternative.
Production Planning
The production process of engine valves plays a significant role in achieving sustainability. Energy efficiency in production processes has yet to receive due consideration, with major energy losses often going unnoticed. A 2013 study argues that energy efficiency should be treated as a major goal in production planning, equal to cost savings. The study proposes methods such as reducing idle time, a significant source of energy waste. Better organization of batches, orders, and shutdowns can minimize idle time, leading to energy savings and the development of efficient methods focused on energy conservation.
Waste Reduction, Reusing, and Recycling
Reducing, reusing, and recycling are fundamental principles of sustainability. Various machining processes, such as grinding and turning, are employed in engine valve production causing staggering rates of material wastage. This can be mitigated by optimizing cutting processes. Closed-loop recycling systems, which focus on reusing scraps to convert them into raw materials, have gained popularity in recent years as a sustainable choice within manufacturing industries.
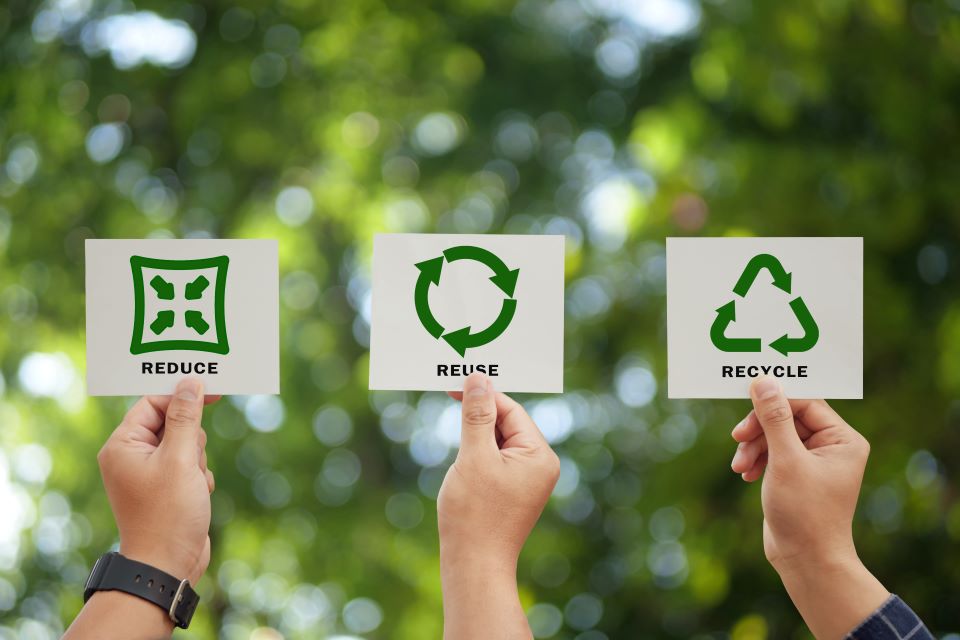
Eco-Friendly Surface Treatments
Surface treatments performed on engine valves are essential for enhancing properties such as wear and corrosion resistance. However, the materials used in these treatments can be replaced without compromising these perks. Chrome plating, a popular surface coating treatment for engine valves, is known for its toxic effect on the environment. Chrome has been classified as a carcinogen, posing risks to both humans and the environment. Alternative methods such as salt bath nitriding and nickel plating have gained acceptance in recent years as more eco-friendly options.
In conclusion, achieving sustainability in engine valve manufacturing does not have to come at the cost of performance. By carefully considering material selection, production planning, waste reduction, and recycling, as well as adopting eco-friendly surface treatments, manufacturers can strike a balance between environmental responsibility and operational efficiency.
Curious to learn about the production process of engine valves? The THORS course, Engine Valve Manufacturing, is a comprehensive and engaging course that explores the process in detail.