Lean manufacturing is a systematic approach to optimizing processes and eliminating waste within manufacturing operations. It aims to maximize value for customers while minimizing resources, time, and effort expended in production, ultimately leading to improved quality. Lean manufacturing principles and practices are crucial for businesses seeking to enhance efficiency, reduce costs, and improve overall productivity. By streamlining processes and eliminating unnecessary steps, lean principles enable organizations to deliver high-quality products or services to customers more efficiently, ultimately leading to increased competitiveness and profitability.
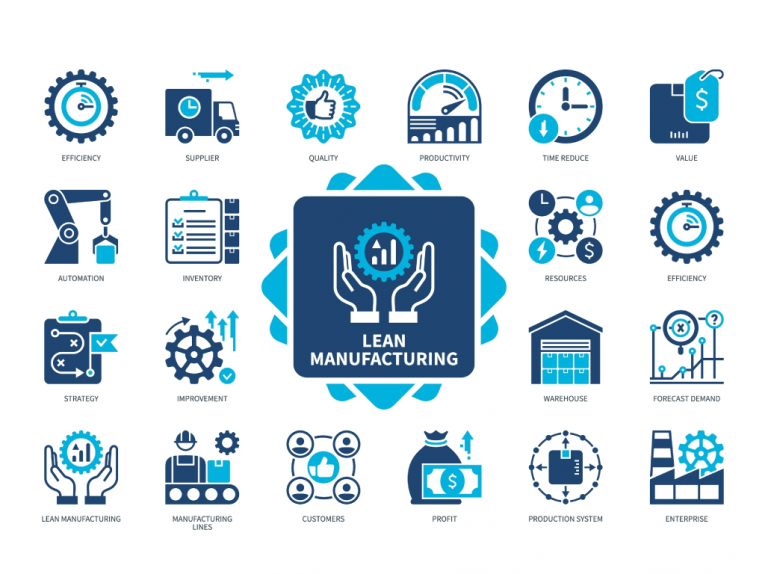
History of Lean Manufacturing
Lean manufacturing principles originated in Japan, notably at the Toyota Motor Corporation. Facing intense competition and limited resources, Toyota recognized the need for a more efficient and cost-effective production system. In response, they developed the Toyota Production System (TPS), which aimed to streamline operations, minimize waste, and maximize productivity. The TPS laid the groundwork for lean manufacturing principles, revolutionizing the way organizations approach production and inspiring a global movement towards lean methodologies.
Lean Manufacturing Principles
Lean manufacturing principles encompass a set of fundamental concepts designed to enhance efficiency, minimize waste, and foster continuous improvement in organizational operations. These principles include a focus on value, value stream mapping, flow, pull, and perfection, each contributing to the overall goal of optimizing processes and delivering greater value to customers.
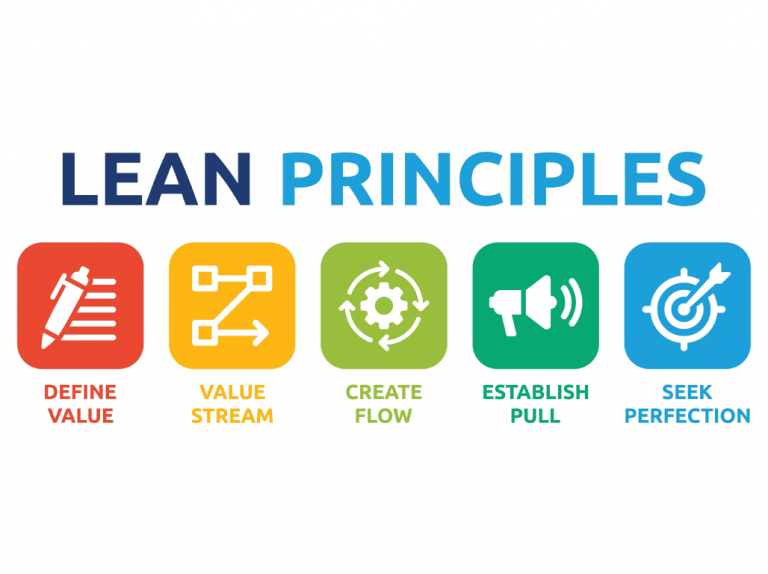
- Value: Lean manufacturing begins with a focus on understanding and delivering value to the customer. By identifying what customers truly value, organizations can streamline their processes to eliminate non-value-added activities, thereby increasing efficiency and reducing waste.
- Value Stream Mapping (VSM): Value stream mapping is a visual representation of all the steps required to bring a product or service from concept to delivery, including both value-adding and non-value-adding activities. By mapping the entire value stream, organizations can identify bottlenecks, inefficiencies, and waste, allowing them to prioritize improvement efforts and optimize the flow of work.
- Flow: Flow in lean manufacturing emphasizes keeping things moving smoothly and continuously throughout the production process. This means minimizing interruptions, speeding up processes, and aligning activities with customer demand. By optimizing flow, companies can cut delays, shorten lead times, and better meet customer needs.
- Pull: Lean manufacturing prefers a pull-based production system. In traditional push-based production systems, manufacturing processes are initiated based on forecasts and inventory levels, rather than actual customer demand. Pull systems respond directly to customer demand, minimizing waste and keeping inventory levels low. Visual cues, like Kanban cards, signal when production is necessary, enhancing efficiency and responsiveness.
- Perfection: Perfection, often referred to as continuous improvement or Kaizen, is the ongoing pursuit of excellence in all aspects of operations. Lean organizations are committed to continuously identifying opportunities for improvement, implementing changes, and measuring results. By embracing a culture of continuous learning and innovation, organizations can adapt to changing market conditions, drive operational excellence, and sustain long-term success.
Practices of Lean Manufacturing
Practices of lean manufacturing encompass a range of strategies aimed at optimizing processes, enhancing productivity, and fostering a culture of continuous improvement within organizations. Let’s delve deeper into each practice to understand their significance in driving operational excellence and achieving organizational goals.
- Just-In-Time (JIT) Production: JIT production is a key practice in lean manufacturing that aims to minimize inventory levels and eliminate waste by producing goods only as needed. By synchronizing production with customer demand, organizations can reduce carrying costs, storage space requirements, and the risk of obsolescence while improving responsiveness and flexibility.
- Kaizen (Continuous Improvement): Kaizen is a philosophy of continuous improvement that encourages all employees, from the shop floor to the executive suite, to identify and implement small, incremental changes to improve processes, products, and services.
- The 5S methodology is a systematic approach to workplace organization and standardization that focuses on Sort, Set in order, Shine, Standardize, and Sustain. By organizing the workplace, eliminating clutter, and establishing visual controls, organizations can improve efficiency, safety, and productivity while reducing the risk of errors and accidents.
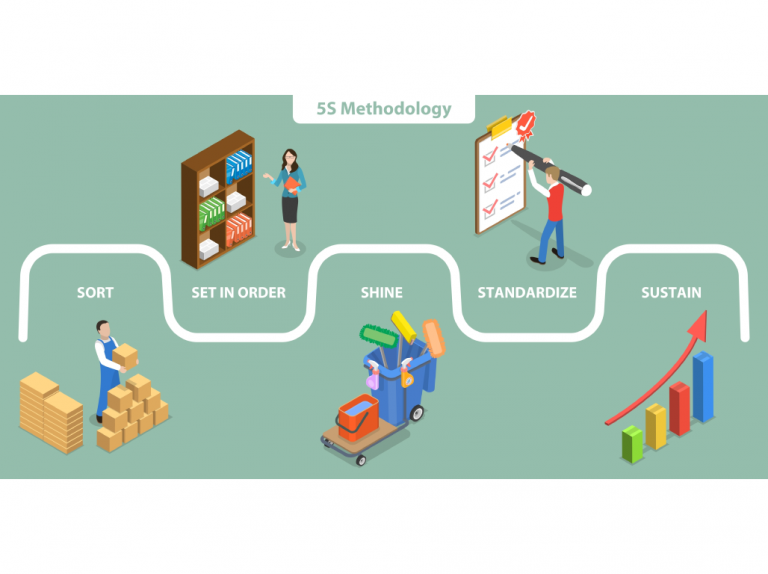
- Total Productive Maintenance: Total Productive Maintenance, or TPM, is a proactive approach to equipment maintenance that aims to maximize equipment effectiveness, minimize downtime, and extend asset life. By involving operators in maintenance activities, implementing preventive maintenance programs, and fostering a culture of ownership and accountability, organizations can reduce unplanned downtime, improve equipment reliability, and optimize overall equipment effectiveness (OEE).
- Error Proofing (Poka-Yoke): Poka-yoke, or error-proofing, is a technique used to prevent errors and defects from occurring in the production process. By designing systems, processes, and tools to make errors impossible or immediately detectable, organizations can improve product quality, reduce rework, and scrap, and enhance customer satisfaction.
- Respect for People: Respect for people is a fundamental principle of lean manufacturing that emphasizes the importance of valuing and empowering employees. By fostering a culture of trust, collaboration, and mutual respect, organizations can unleash the full potential of their workforce, encourage innovation and creativity, and create a supportive environment.
Lean manufacturing principles and practices serve as foundational pillars for organizations aiming to optimize operations and meet customer needs efficiently. By emphasizing continuous improvement, waste reduction, and employee empowerment, businesses can streamline processes, enhance productivity, and remain competitive in dynamic market environments.