What are the Primary Gear Hobbing Cutting Parameters?
Primary gear hobbing cutting parameters include the radial feed rate, the axial feed rate, the work spindle speed, or work spindle revolutions per minute (rpm), and the hob spindle speed, or hob spindle rpm. Hob Surface Footage per Minute, or SFM, is also an important variable to understand. Finally, selecting the right cutting oil and the correct oil flow rate is crucial to successful gear hobbing operations.
- The radial feed rate, also referred to as the depth of cut feed rate, or just the feed rate, is the speed at which the hob moves in the X-axis direction to control the depth of cut of the gear tooth.
- The axial feed rate is the rate of linear travel, typically in the Z-axis, across the length of the gear blank, also referred to as the face width.
- The work spindle speed is the rate at which the work spindle turns the workpiece.
- The hob spindle speed is the rotational rate at which the hob spins.

How are Hob Spindle Speed and Surface Footage per Minute Determined?
The formula for hob spindle speed is 3.82 times the or SFM, divided by the hob diameter. Inversely, the formula to calculate hob SFM when the rpm is known is as follows: π, or 3.14, times the hob diameter, times the rpm divided by 12. The typical SFM ranges from 80 SFM to 800 SFM and can run as high as 1,500 SFM. It is important to calculate the correct SFM based on the material of the gear blank and material of the cutting hob to select the correct hob spindle speed.
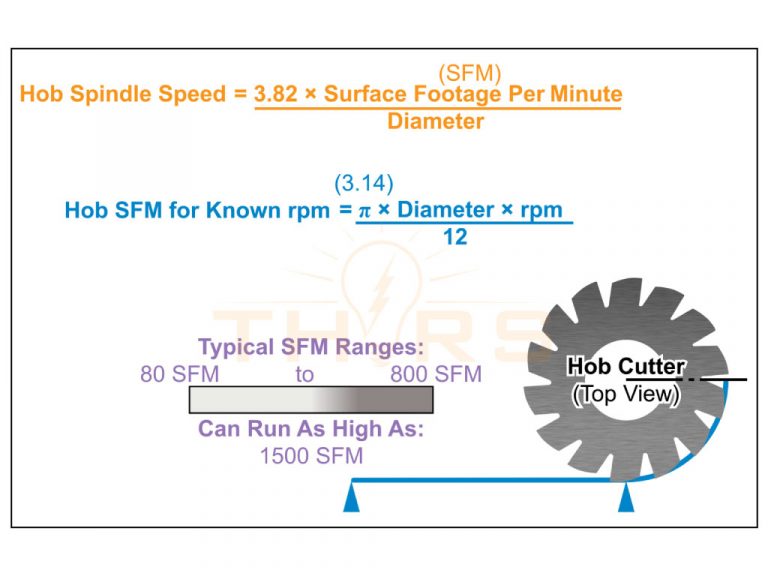
What Type of Coolants are Used in Gear Hobbing?
Gear hobbing cutting parameters require that most gear hobbing operations use cutting oil as a coolant; however, other options are available. It is important to understand both the advantages and disadvantages of the various types of coolant. It is also important to ensure that the correct coolant flow rate is selected for each operation. This is required for both accurate cutting and so that the chips are sufficiently flushed away from the workpiece and hob.
- Cutting oil provides the best lubricity, offers moderate heat transfer, and flushes away the chips created during the hobbing process.
- Synthetic-based coolants are also used in the hobbing process. Synthetic-based coolants offer some lubricity, provide excellent heat transfer, and flush chips away from the workpiece and hob. However, synthetic-based coolants do not offer rust-preventative characteristics to the workpiece.
- Soluble oils and semisynthetics offer better lubricity and some rust-preventative characteristics, compared to synthetic coolants, but require more maintenance and lack the heat transfer characteristics of synthetics and cutting oils.

Learn more about gear hobbing cutting parameters in THORS’ Gear Hobbing Video Series 2.