Course Description
8D Problem-Solving Basics introduces learners to the popular “8 Disciplines,” commonly referred to as 8D. The 8D problem-solving methodology is an important quality tool utilized in a variety of industries. Presented in THORS’ highly visual and interactive learning format, this course will help employees become familiar with the important terminology and methodology associated with 8D implementation.
Who will benefit from this 8D Problem-Solving course?
Any individual, team, or organization involved in quality assurance processes. Though the examples in this course pertain to the manufacturing industry, the problem-solving methodology is universal, and can apply to anyone who seeks to approach problem solving with a scientific, systematic, proven methodology.
Course Classification
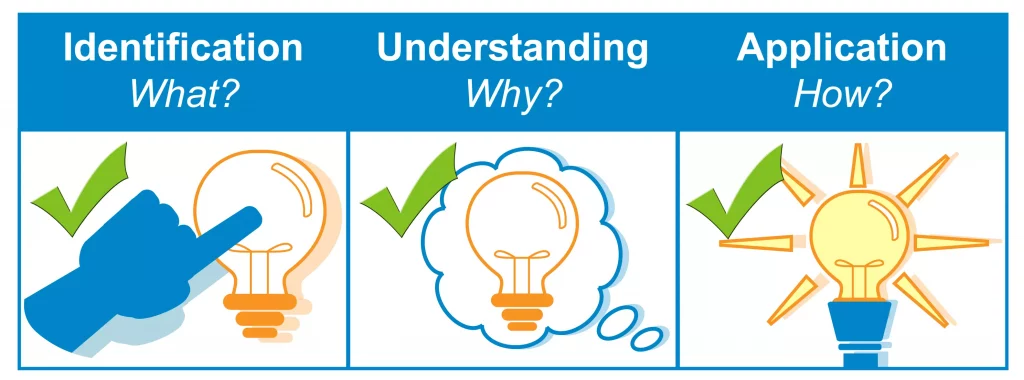
*THORS uses the Bloom’s Taxonomy Methodology for our course development.
Certificate Awarded for 8D Problem-Solving Basics

*upon successful completion
Related Posts
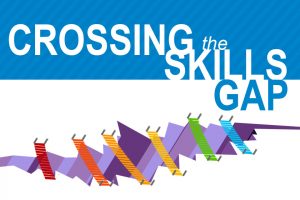
Is Your Issue a Skills Gap or a Knowledge Gap?
You may have received a call to action to address the skills gap, which might feel making a bridge across the Grand Canyon with a
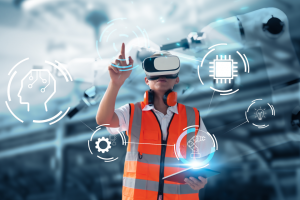
The Role of Virtual Reality in Technical Training
In the rapidly evolving landscape of technology and industry, virtual reality (VR) in technical training is leading a revolutionary transformation in how professionals are trained.
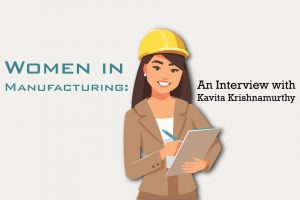
Women in Manufacturing: An Interview with Kavita Krishnamurthy
As part of a tribute to women in manufacturing, we at THORS eLearning Solutions decided to showcase one of our own, Kavita Krishnamurthy. Kavita is