What is Takt Time in Manufacturing?
Takt time for manufacturing, also known as takt, is a term that describes the time available to complete a task divided by the customer demand for the service or product. In a mass-production sense, implementing takt time requires adjusting product assembly time to satisfy the demand, and doing so in a way that is efficient and profitable. Takt time is applied in numerous industries, including shipping, data analysis, manufacturing, and project management.
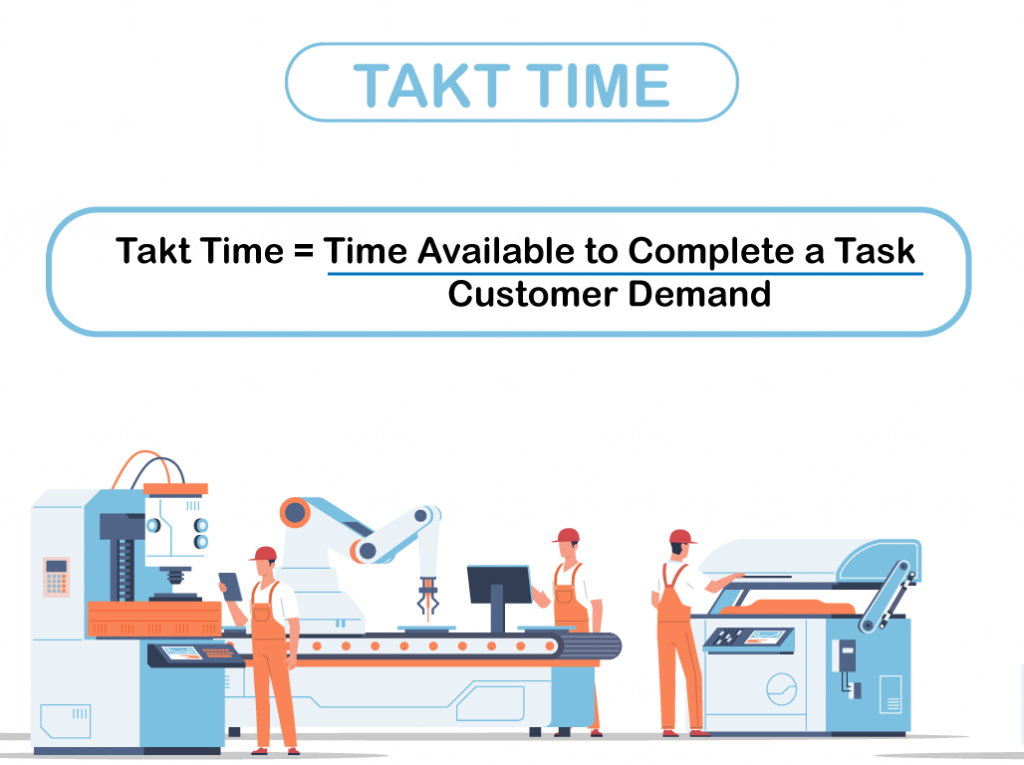
How is Takt Time Calculated?
Takt time for manufacturing is calculated by dividing net available time, or time available for the task, by customer demand, or the quantity of products required by the customer. The formula to calculate takt time may be represented with symbols:
- “T” stands for takt and represents the work time between products,
- “Ta” stands for net available time, or the work time available, and
- “D” stands for demand, or the quantity of parts required.
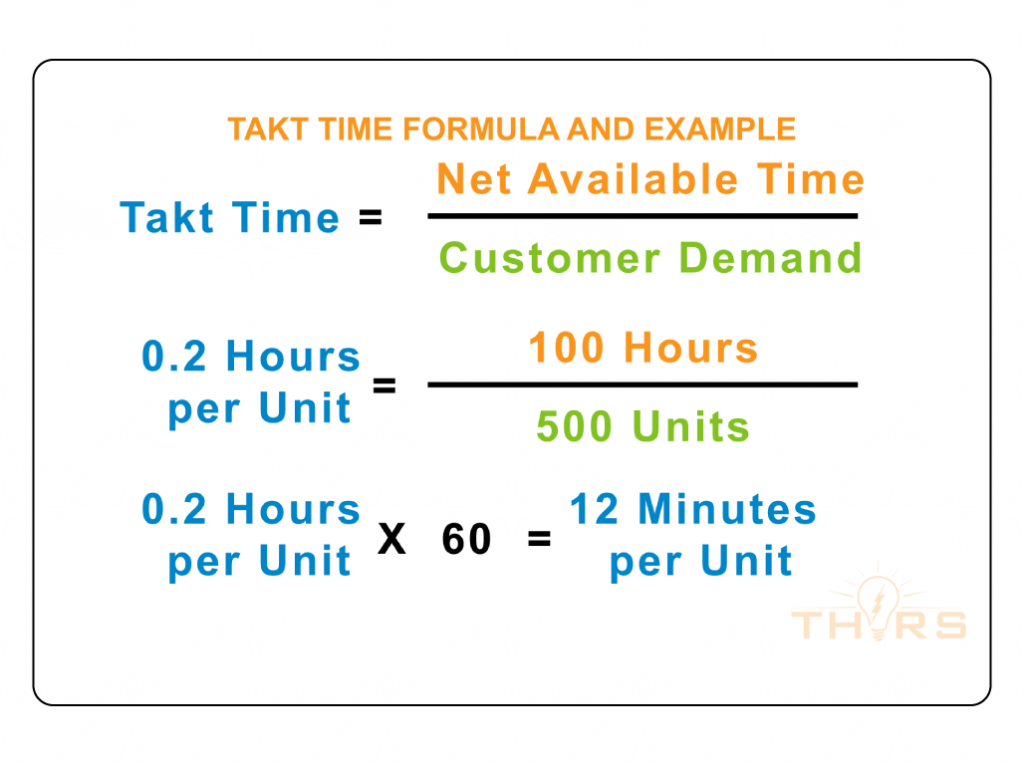
What is the Focus to Implement Takt Time?
Implementing takt time requires a mindset that focuses on customer requirements. The goal of producing as many parts as possible should be replaced with a focus on meeting customer expectations in repeatable timeframes. Implementing takt time also requires that the proper production steps are constantly adjusted to work in tandem with customer demand. The cost of implementing takt time varies depending on the level of automation involved, the manufacturing capacity of the company, and the requirements of the process.
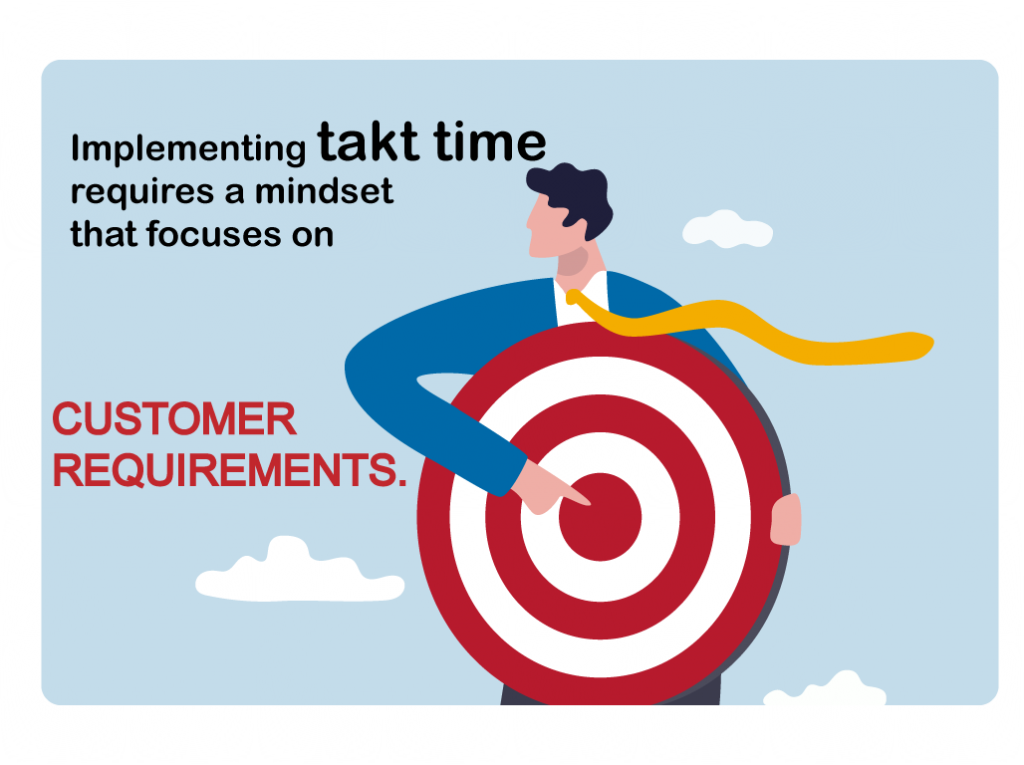
What are the Steps to Implement Takt Time?
- The first step is to identify customer demand to properly satisfy their requirements over a specified period.
- The second step is to calculate the takt time by dividing net available time by customer demand.
- The third step is to establish flow to ensure that all team members understand their roles and responsibilities and that everyone works toward the same goal.
- The fourth step is to eliminate waste by monitoring and eliminating issues such as overproduction, excessive wait times, part defects, unused inventory, wasted movement, and untapped employee creativity.
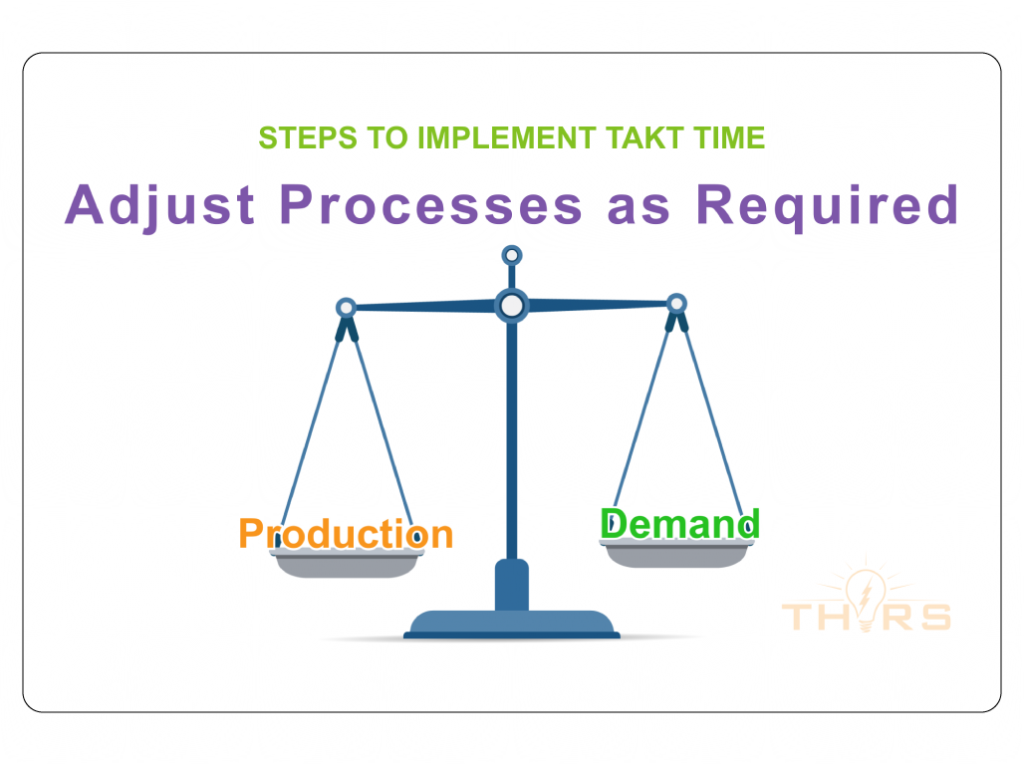
Understanding the basic calculation and implementation of takt time is an important step for improving manufacturing efficiency and productivity. However, manufacturers must also be aware of many other variables regarding the manufacturing facility, the machinery and equipment being used, and the order of operations involved, to ensure improvements with takt time.
THORS presents the crucial aspects of implementing takt time for manufacturing in our visual and interactive learning format. In addition, we have a diverse manufacturing excellence library covering a variety of improvement methods used in manufacturing industries. Visit thors.com to expand the knowledge and skillsets of your workforce, and to ensure that your company has the highest quality training available today.
Check out our course, Takt Time here.