What is cycle time?
In manufacturing, cycle time is the time spent within a single operational step during the process of making a complete product or providing a service. The concept of cycle time was created in the 1920s by the Ford Motor Company to reduce the time it took to manufacture an automobile. Since then, cycle time has become a widely used metric for manufacturing efficiency and operational excellence in manufacturing, software engineering, and many other industries.
Check out our course introduction video here.
How is cycle time for manufacturing calculated?
Cycle time for manufacturing is calculated by dividing the net production time by the number of units produced during that time. Assume an auto manufacturer can produce 100 vehicles over a 40-hour work week. The total number of hours spent on net production is then divided by the number of units required, resulting in a total of 0.4. So, the cycle time in this example for producing 100 vehicles is 0.4 hours per unit. On average, it takes 0.4 hours, which equals about 24 minutes, to manufacture one vehicle.
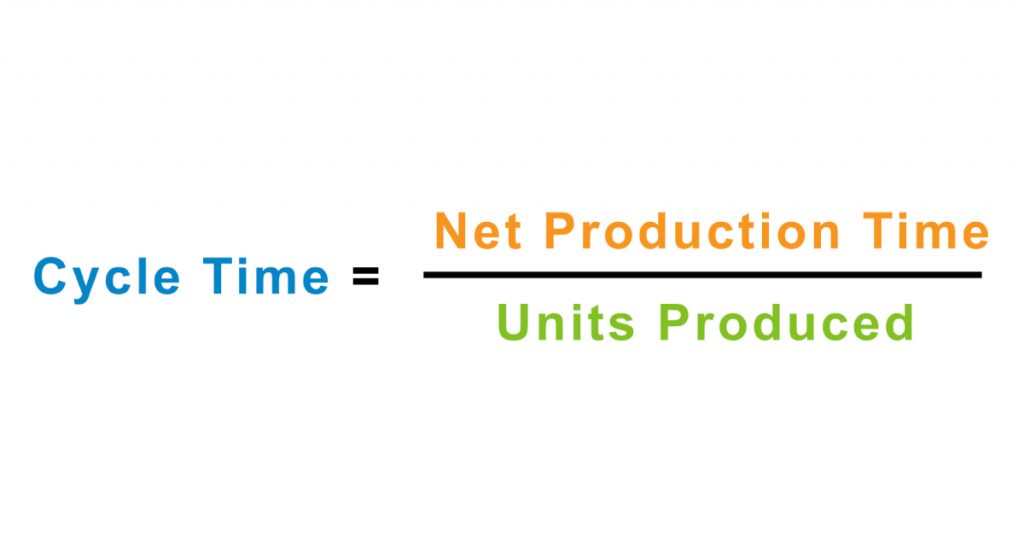
How is Manufacturing Cycle Efficiency (MCE) calculated?
Manufacturing Cycle Efficiency, or MCE, is a cycle time-adjacent metric that focuses on the efficiency of processes. MCE is calculated by taking the time spent on activities that add value and dividing by the manufacturing cycle time, including all steps in the process. Activities that add value are those that are required to deliver quality products in a timely manner, or activities that help improve the process. Activities that do not add value to the process should be eliminated or reduced as much as possible.

What are the six steps to follow when implementing cycle time?
To implement cycle time in manufacturing, organizations should follow these steps.
- Identify the process, which could be a specific production line, a particular product, or a specific service.
- Define the scope of the process, which could include the number of people involved, the equipment used, and the materials required.
- Map the process, which will help identify the steps involved and how each step relates to the others.
- Identify the tasks involved in the process, including tasks such as assembly, inspection, and packaging.
- Monitor the time it takes to complete each task, which will help identify the total cycle time for the operation.
- Analyze the data, which helps identify areas of potential improvement.
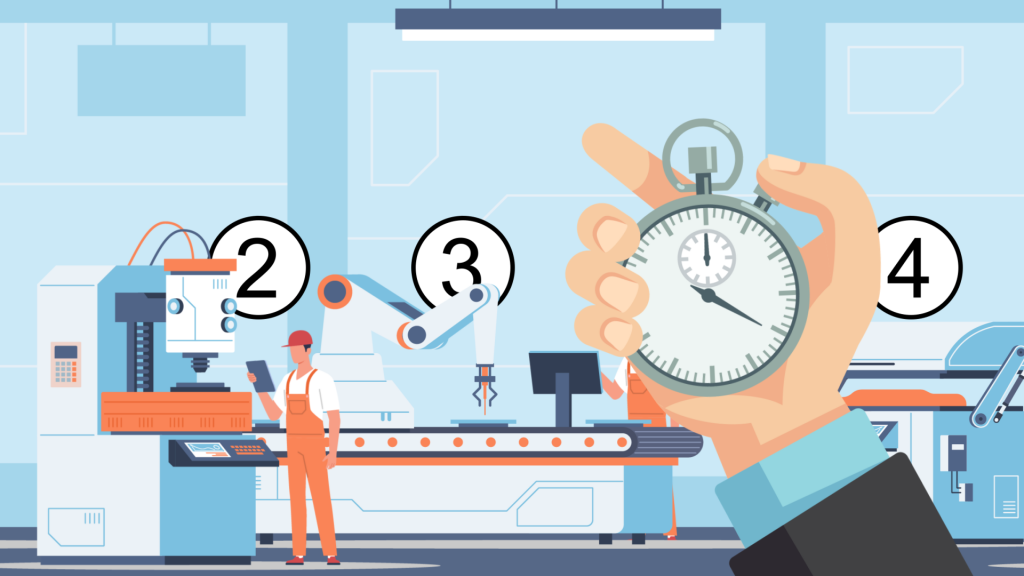
Understanding the basic calculation and correctly monitoring cycle time are important steps for improving manufacturing efficiency. However, manufacturers must also be aware of many other parameters involved in their processes. Improvements to cycle times will only be successful if team members have a strong understanding of the equipment and processing steps involved in their operations.
THORS presents these crucial aspects of implementing cycle time for manufacturing in our visual and interactive learning format. Check out the course here.
In addition, we have a diverse manufacturing excellence library covering a variety of improvement methods used in manufacturing industries. Visit thors.com to expand the knowledge and skillsets of your workforce, and to ensure that your company has the highest quality training available today.