First, let’s establish a few definitions since these terms are often used interchangeably, however there are some key differences.
Cathodic Electrodeposition, or CED, painting is a process where a metal part is coated with paint using an electrochemical reaction to achieve a uniform and durable coating.
Electrocoating is the more general term for applying coatings to a substrate using electrical currents and encompasses other cathodic processes as well as anodic processes.
Electroplating is an anodic coating process that involves metal deposition rather than paint.
Powder Coating involves coating a part with an electrostatically charged dry powder first, then heating to melt and cure the powder.
Cathodic Electrodeposition (CED) painting has emerged as the preferred method for surface protection due to its excellent deposition and superior corrosion resistance, establishing CED as a gold standard in corrosion prevention. CED painting has gained acclaim across various sectors, from automotive manufacturers to agricultural equipment manufacturers. This article delves into the innovative aspects of CED painting technology and its implications for various industries.
Understanding CED Painting
CED painting employs a Direct Current (DC) to deposit a water-based paint solution onto a metal part. This process takes place when the metal part is immersed in a CED tank containing a paint solution. By applying a DC voltage to the metal part, paint particles adhere uniformly to the metal surface, providing a high quality finish with excellent adhesion properties. Watch our video on Youtube, What is Cathodic Electrodeposition (CED) Painting?
In addition to delivering a consistent coating, CED painting offers excellent durability by minimizing the chances of mechanical damage, such as scratching and chipping. The comprehensive coverage it achieves, including intricate areas, prolongs the lifespan of the painted part. Industries from automotive to appliance manufacturing have benefited from implementing this technology, enhancing product durability and dependability. To learn more about CED painting systems, equipment, and processes, check out our online course, Cathodic Electrodeposition (CED) Painting Basics, in the THORS Academy.
Environmental and Economic Advantages
The environmental benefits of CED painting are significant. Traditional paint application methods often employ solvents that emit Volatile Organic Compounds ( which contribute to air pollution, during the painting process. In contrast, CED painting utilizes zero VOC paint formulations, which produce much less VOC emissions. This shift aligns with global efforts to minimize ecological impact, leading to sustainable manufacturing.
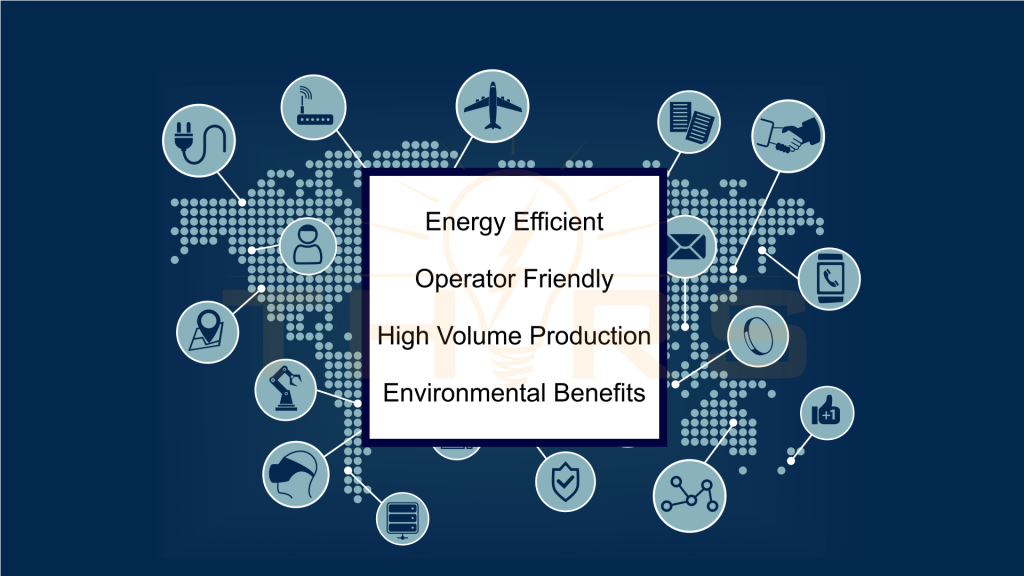
Global Efforts to Minimize Ecological Impact
While initial setup costs for CED painting systems are significant, the long-term benefits create compelling economics. A detailed analysis of manufacturing facilities implementing CED coating reveals the following:
- Reduction in coating material waste through precise deposition control
- Decrease in warranty claims related to corrosion issues
- Lower energy consumption compared to conventional painting systems
- Faster processing times due to automated handling and efficient curing
- Reduction in touch-up requirements
- Improvement in overall product lifespan
- Reduction in maintenance costs through simplified cleaning procedures
The automotive sector in particular benefits from the ability of to protect complex assemblies, with modern vehicles achieving 12+ years of corrosion protection even in harsh environments.
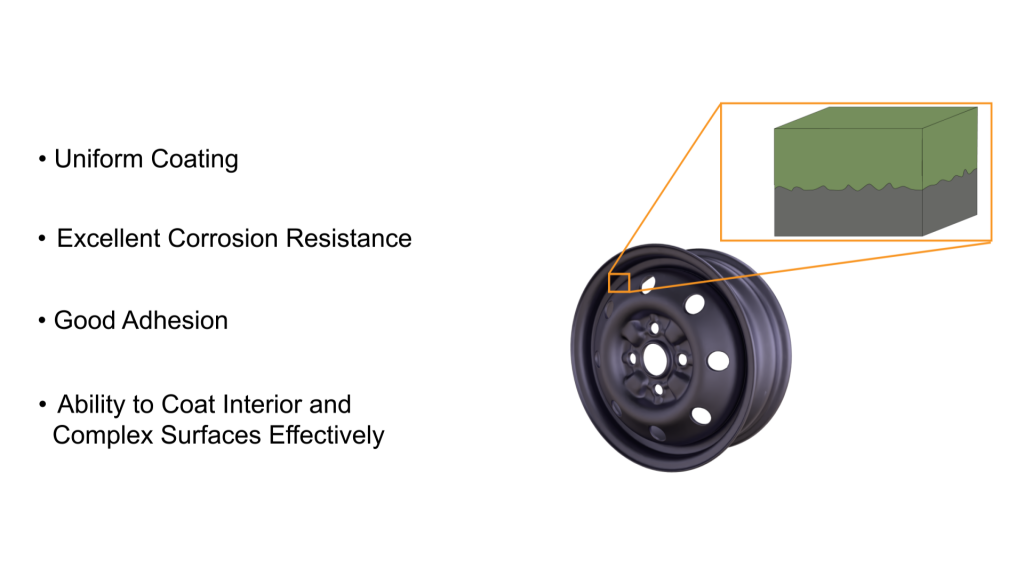
Recent Innovations for Superior Protection
Modern CED paint formulations contain specially engineered epoxy or acrylic resins, cross-linking agents, pigments, and catalysts. During deposition, these components create a uniform paint film that chemically binds with the metal part. The chemical reaction at the surface creates a pH gradient that forms cross-linked networks during curing, creating an impenetrable barrier against moisture, chemicals, and environmental contaminants.
Recent innovations include:
- Self-healing properties that activate when the coating is scratched, utilizing microcapsules containing reactive healing agents
- Enhanced edge protection achieving up to 98% coverage on sharp edges
- Low temperature curing capabilities that reduce energy consumption while maintaining coating integrity
- Smart additives that signal coating breakdown before corrosion begins through color changing indicators
- Zero Volatile Organic Compound (VOC) paint formulations meeting strict environmental standards without compromising on the coating properties
- Nanoengineered additives that enhance scratch resistance and UV stability
- CED-coated parts consistently survive 1,000+ hours in salt spray testing, far exceeding 400-500 hour protection offered by conventional coating technologies
- Superior impact resistance withstanding direct forces up to 160-inch pounds without compromising coating integrity through cracking or separation from the substrate
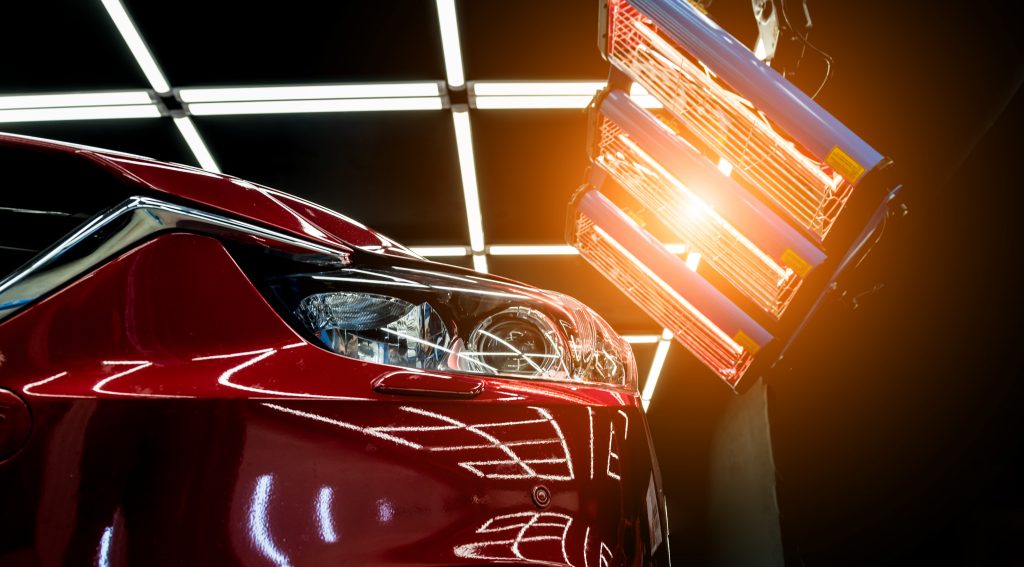
The Future of CED Painting
As advancements in paint formulations, automation, and surface preparation techniques continue to progress, the potential applications for CED paintings are extensive. Industries are likely to witness a shift toward adoption of CED painting in applications ranging from consumer goods to aerospace components. The future of CED painting technology appears promising, underscoring its importance in the quest for sustainable and high-performance manufacturing solutions.
To learn more about CED painting systems, equipment, and processes, check out our Cathodic Electrodeposition (CED) Painting Basics online course.
To learn more about other manufacturing processes and products, check out our THORS Academy Course Library today!